1. LE BOIS LAMELLÉ-COLLÉ EN TANT QUE MATÉRIAU DE CONSTRUCTION
1.1. INTRODUCTION
Le bois lamellé est un composant bois de haute technicité. L’utilisation de lamelles en bois classées selon leur résistance et assemblées par entures multiples permet de fabriquer des poutres de presque toutes les tailles et toutes les formes. Basé sur l’utilisation du seul matériau de construction réellement renouvelable – le bois –, le lamellé possède des avantages indéniables sur le plan environnemental.
Le bois lamellé se caractérise par une résistance et une rigidité excellentes comparées au bois de sciage de mêmes dimensions. Ce matériau se distingue par un rapport résistance/poids exceptionnel : à résistance égale le bois lamellé se révèle nettement plus léger que les autres matériaux de structure, comme l’acier, ce qui lui permet d’importants franchissements, et en conséquence de grandes structures. Il est ainsi techniquement possible d’obtenir une portée de 150 mètres, voire davantage.
La possibilité de concevoir librement la forme de la section combinée à la possibilité d’utiliser des poutres à inertie variable ou courbes et de concevoir des structures à grande portée a ainsi motivé le choix du bois lamellé dans de nombreux projets à haute valeur architecturale.
À l’heure actuelle, le bois lamellé est utilisé pour tout type de construction, notamment pour les immeubles d’habitations multi-étages, les bâtiments d’activités et immeubles de bureaux, les halls, les stades de sport, les piscines, les ponts routiers ou encore les maisons. Lorsque la conception, les détails et la protection contre les intempéries sont appropriés, le bois lamellé se prête à la plupart des applications.
1.2. RAPPELS SUR L’HISTOIRE DU MATERIAU*
Si l’on retrouve des traces du procédé propre au bois lamellé dès le 12ème siècle au Japon, c’est à l’architecte français Philibert De l’Orme (conseiller du roi Henri II et responsable des chantiers royaux) que l’on doit le procédé de lamellation, qui annonce les prémices du bois lamellé en Europe. En 1548, l’architecte met en place un procédé – reposant sur des lamelles de courtes sections solidarisées par clavetage - afin de réaliser des charpentes en voutes.
De multiples évolutions et déclinaisons (notamment s’agissant de l’assemblage des lamelles) interviennent au cours des siècles en Europe. En France, c’est le Colonel Émy qui, au XIXe siècle, opère une synthèse de ces expériences pour faire avancer encore le procédé de fabrication de ce matériau, afin de réaliser nombre de manèges. Il aboutit ainsi à l’empilement de planches disposées horizontalement et cintrées perpendiculairement à leur plan ; les joints sont décalés. Ces planches sont serrées par des liens moisants, alternés avec boulons et colliers en acier. Le procédé qui fut appliqué au manège de Libourne en 1821 et à celui de Bayonne en 1826 avec des portées de 21 mètres.
Mais c’est à Otto Hetzer (1846-1911), charpentier, ingénieur, propriétaire d’une scierie et inventeur de Weimar, que l’on doit l’invention proprement dite du « bois lamellé collé ». Dans le brevet DRP n°197773 de 1906, Hetzer décrit comment construire des poutres lamellées de forme courbe : les « Hetzer binder ». La colle utilisée était à base de caséine (à partir des protéines du lait). Le « Reichseisenbahnhalle », réalisé à l’occasion de l’Exposition universelle de Bruxelles de 1910, est l’une des premières structures en lamellé-collé d’importance. Sa charpente, composée d’arcs et dotée de tirants, présentait une portée libre de 43 mètres. À l’époque, Hetzer avait déjà réalisé une cinquantaine de structures de relativement grande portée, mais cette réalisation, par son caractère exceptionnel et la liberté accordée à la forme par la haute technicité du matériau, marqua une étape décisive.
Après l’invention à Weimar et son industrialisation par Otto Hetzer, la technique du bois lamellé se développa rapidement (dès 1910) en Suisse puis au Pays-Bas ; puis dans les pays du Nord de l’Europe (dès 1918). Guttorm Brekke, employé en tant qu’ingénieur au sein de la société Otto Hetzer AG, acquit les droits pour la Norvège, la Suède et la Finlande. Il installa une usine de fabrication de la poutre Hetzer binder à Mysen, en Norvège : la Trækonstruktioner A/S, qui deviendra à la fin des années 1950 Moelven (très active aujourd’hui encore). Une filiale suédoise est créée en 1919. Parmi les premières structures en bois lamellé-collé réalisées en Suède, il convient de citer les halls des gares centrales de Stockholm, Göteborg et Malmö.
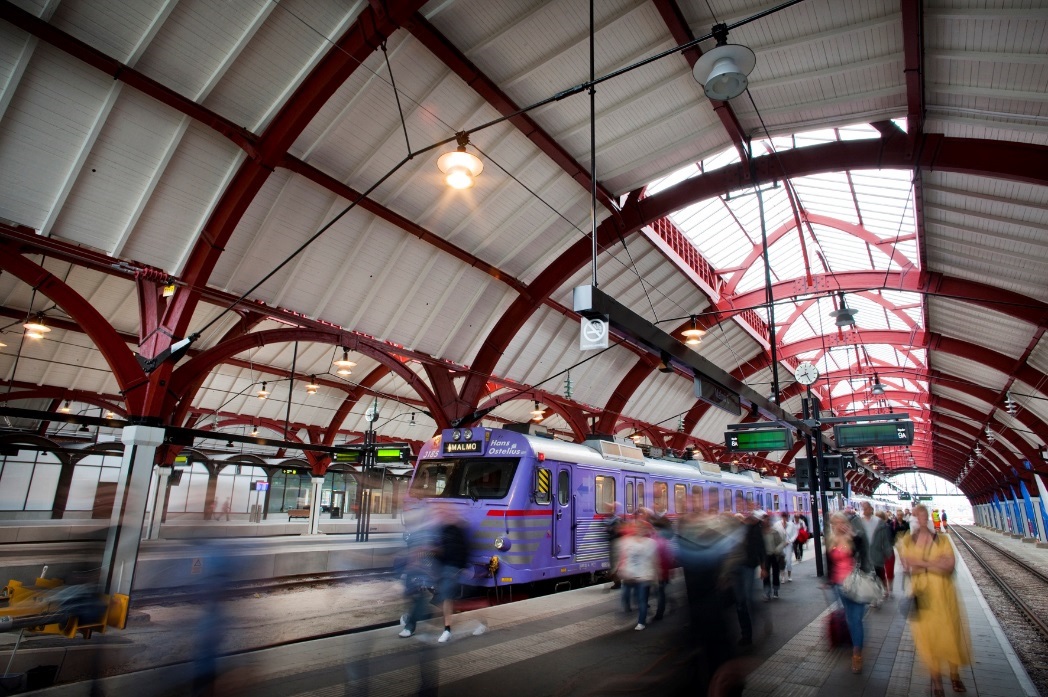
Figure 1.1 : Principal hall de la gare centrale de Malmö (Suède), construit en 1923. Le bâtiment de la gare remplit encore pleinement ses fonctions. Architecte : Folke Zettervall, SJ Arkitektkontor, Suède.
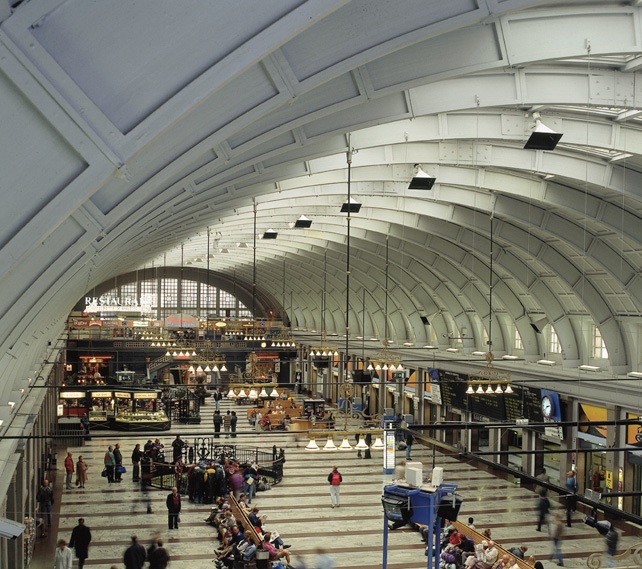
Figure 1.2 : Gare centrale de Stockholm – le principal hall actuel a été construit en 1925. Architecte : Folke Zettervall.
Si Suède et Norvège ont largement consolidé leur position de précurseurs au cours des décennies qui ont suivi, une seconde étape a vu, au cours du XXe siècle, d’autres pays se joindre à la dynamique. L’Amérique du Nord importa le concept au milieu des années 30 (aux Etats-Unis, dans un premier temps, le Canada suivra ensuite). Le procédé s’est réellement développé outre-Atlantique entre les années 1950 et 1970. En Finlande, la production de bois lamellé a débuté en 1945, avec la fabrication par la société Oy Laivateollisuus AB des premières coques de navires en bois lamellé destinés à l’URSS en tant qu’indemnités de guerre. C’est un peu plus tard, à partir de la fin des années 1950 (1958) que le bois lamellé a débuté une percée dans l’industrie du bâtiment.
En France, c’est après la seconde guerre mondiale que le procédé revient sur sa terre d’origine. Les premières applications industrielles apparaissent dans les années 1950 et des usines commencent à apparaître. Le développement de cette industrie est intimement lié à la nécessité de reconstruction et d’équipement du pays, largement soutenu par les politiques publiques. Entre les années 60 et 80, nombre de complexes sportifs, salles polyvalentes, bâtiments d’enseignement… ont été édifiés avec le bois lamellé, permettant ainsi à l’industrie de se développer.
*) Pour plus de détails, se reporter au Volume 1
1.3. MARCHE ET ATOUTS DU BOIS LAMELLE COLLE
1.3.1. Évolution de la production de bois lamellé collé
La production de bois lamellé dans le monde, relativement faible jusqu’au début des années 60, a notablement augmenté depuis. On peut ainsi citer en exemple une production des pays nordiques estimée au-delà de 200 000 m3 en 2012 (dont près 50% sont exportés) ; une production française estimée à 180 000 m3 en 2013.
La plus grande partie du bois lamellé utilisé en France est destinée à des bâtiments d’activité (bâtiments industriels, logistiques, tertiaires et centres commerciaux), des bâtiments d’équipement (écoles, piscines, gymnases, stades, parkings) et des logements. On note une tendance récente, en France comme dans de nombreux autres pays, vers les immeubles résidentiels multi-étages. Un usage plus important à ce jour dans les pays scandinaves (où ce type de bâtiments représente 60 % des applications du bois lamellé sur des réalisations de moyenne hauteur), tandis qu’elle est en plein développement en France.
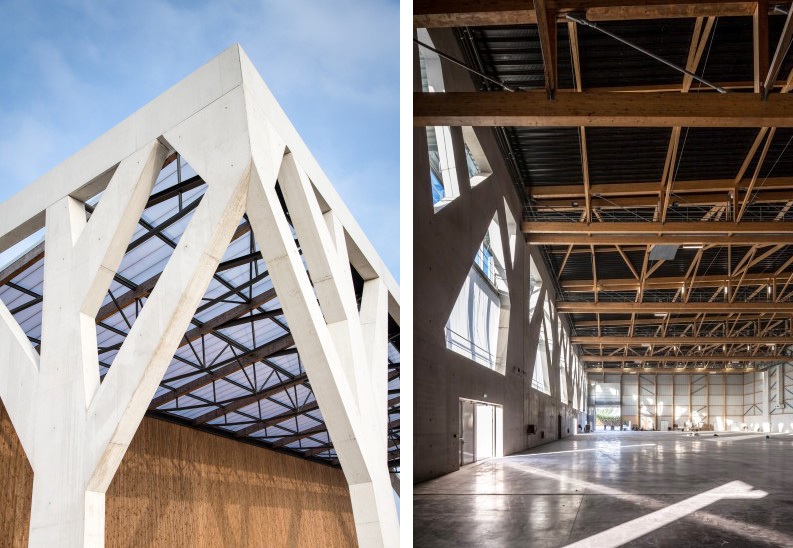
Figure 1.3 : Parc des expositions de Quimper, 2014. Architectes : Philippe Brulé.
1.3.2. Des atouts indéniables
La technique de collage moderne et les excellentes caractéristiques de résistance du bois font du bois lamellé un matériau de construction hautement performant, doté de caractéristiques exceptionnelles :
› Aspect séduisant et moderne, qui confère une valeur ajoutée à l’environnement intérieur et extérieur,
› Rapport résistance/poids élevé, qui permet la construction de structures à grande portée,
› Exigences de fabrication élevées et bonne stabilité dimensionnelle dans des conditions normales de température et d’humidité,
› Haute résistance au feu, exigence essentielle pour les bâtiments publics et ERP,
› Propriétés thermiques satisfaisantes : il réduit l’effet des ponts thermiques ainsi que le risque de condensation,
› Léger, le bois lamellé va de pair avec de faibles coûts de transport et de montage et impacte ainsi favorablement le coût et la complexité des fondations,
› Durable et notablement résistant aux ambiances agressives (y compris chimiquement agressives),
› Production flexible, la fabrication d’éléments structuraux courbes en bois lamellé est économiquement très satisfaisante comparée à d’autres matériaux.
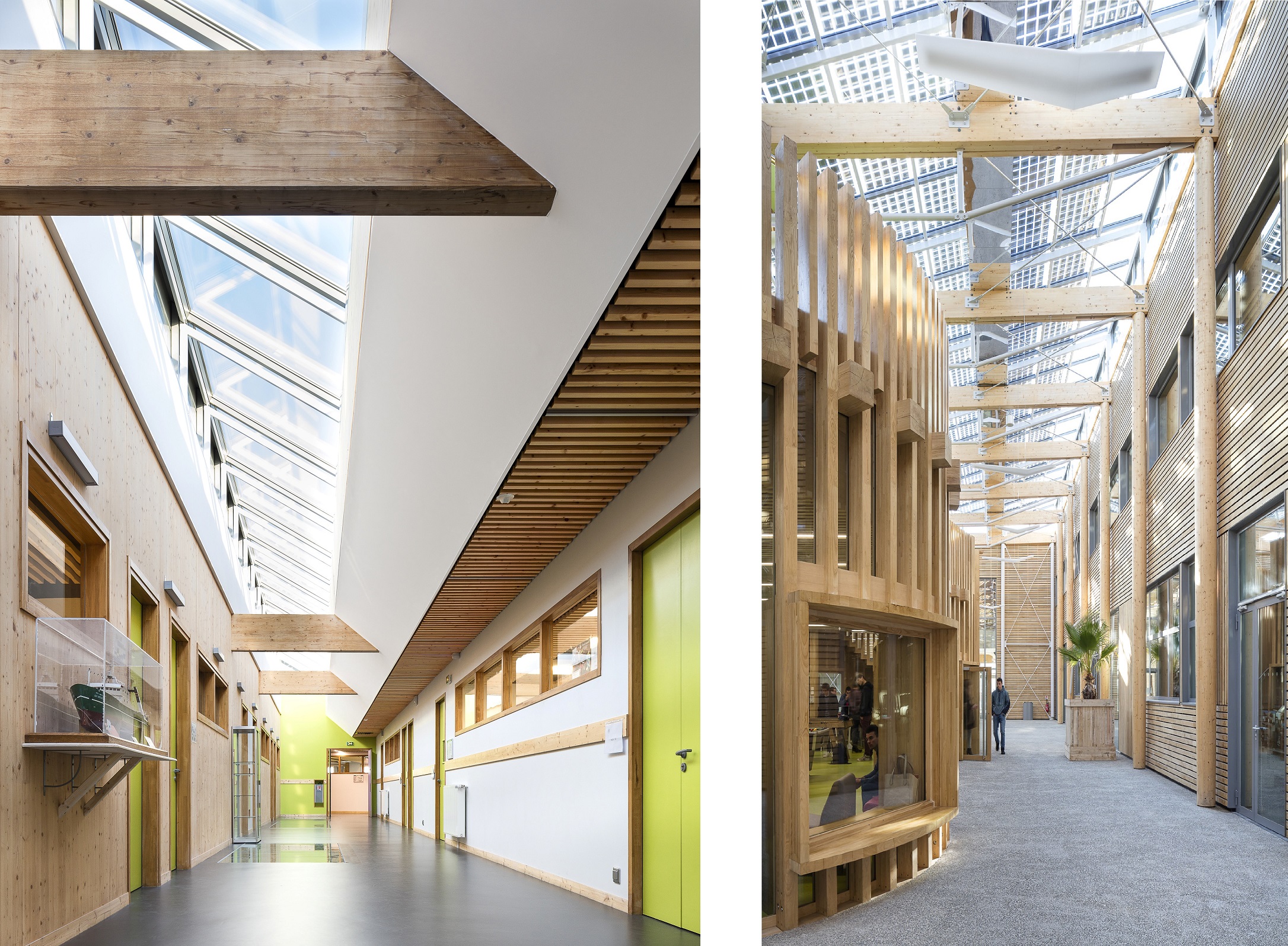
Figure 1.4 : Lycée professionnel maritime Florence Arthaud, de Saint-Malo, livré en 2015. Architecte : Liard & Tanguy.
1.3.3. Assemblages
Les structures en bois lamellé se caractérisent par un montage rapide et simple d’éléments préfabriqués. Ces éléments peuvent être assemblés à l’aide de méthodes traditionnelles simples, et notamment par clouage, vissage ou boulonnage, quel que soit le moment de l’année ou les conditions climatiques. Outre ces moyens traditionnels, il existe, pour les situations plus exigeantes, des méthodes plus sophistiquées qui utilisent, par exemple, des plaques métalliques et des goujons insérés ou des goujons collés.
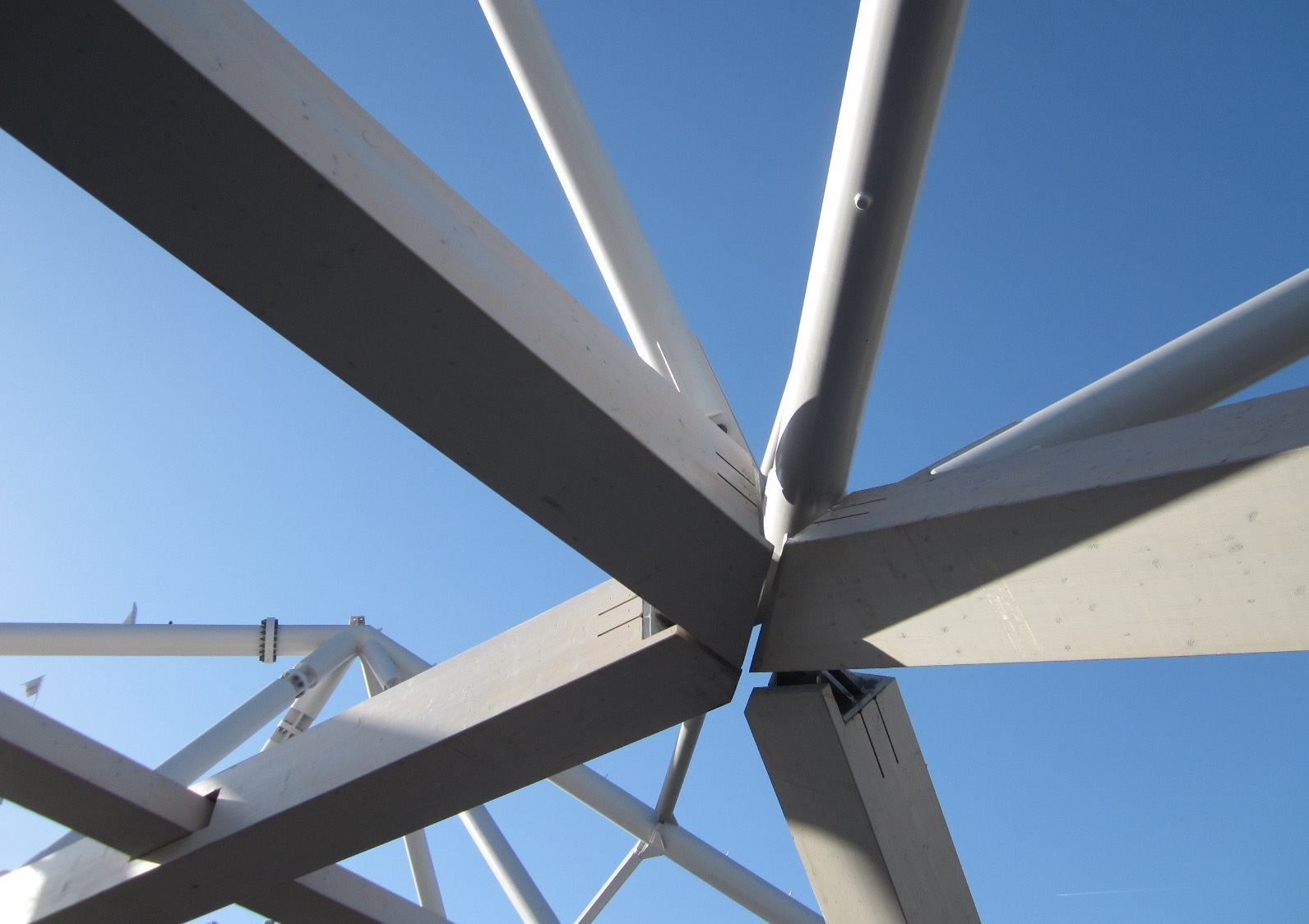
Figure 1.5 : Assemblages de la résille de bois dessinée par le stade Allianz Riviera de Nice, 2013, arch.. Wilmotte & ass.
1.3.4. Chantier sec, structure hautement performante
Une structure en bois lamellé peut supporter sa pleine charge immédiatement après son montage et, s’agissant d’un matériau à base de bois, tout ajustement nécessaire sur place peut être effectué à l’aide de simples outils à main.
Ces structures relèvent d’une méthode de construction sèche et une protection appropriée contre les intempéries est nécessaire, ce qui procure des avantages concernant l’environnement de travail.
1.4. LE CYCLE DE VIE DU BOIS LAMELLÉ
1.4.1. Ressource forestière et puits de carbone
Combinée à des politiques favorables à une gestion forestière durable, comme cela est le cas en France, l’utilisation du bois dans la construction présente des avantages considérables en termes d’impact environnemental et climatique comparé à l’utilisation d’autres matériaux de construction. Premièrement, la fabrication de bois lamellé ne nécessite que peu d’énergie. Deuxièmement, les sous-produits dérivés de la fabrication, tels que la sciure et les copeaux de bois, sont utilisés pour produire de l’énergie (pour chauffer les séchoirs par exemple), et remplacent donc les combustibles fossiles. Enfin, la gestion durable des forêts favorise un renouvellement constant et se révèle bénéfique à la croissance des forêts. Le bois lamellé est en outre recyclable et valorisable, et ces réutilisations n’ont pas d’impact sur le changement climatique (lié aux émissions de gaz à effet de serre).
Au cours de sa croissance, un arbre absorbe du CO2 sous l’action de la photosynthèse. Le carbone est alors stocké dans le bois (et demeure séquestré plusieurs décennies, une fois mis en œuvre, sous forme de bâtiments, par exemple). L’augmentation de l’utilisation de bois dans le secteur de la construction, en remplacement d’autres matériaux moins efficaces sur le plan climatique, permet ainsi de créer un puits de carbone temporaire. Même si la durée de vie de ce puits de carbone est limitée (50-100 ans), il réduit temporairement l’émission nette de gaz à effet de serre. Un mètre cube de bois lamellé prélève environ 800 kg de CO2. Le cycle de vie du bois lamellé est représenté sur la figure suivante.
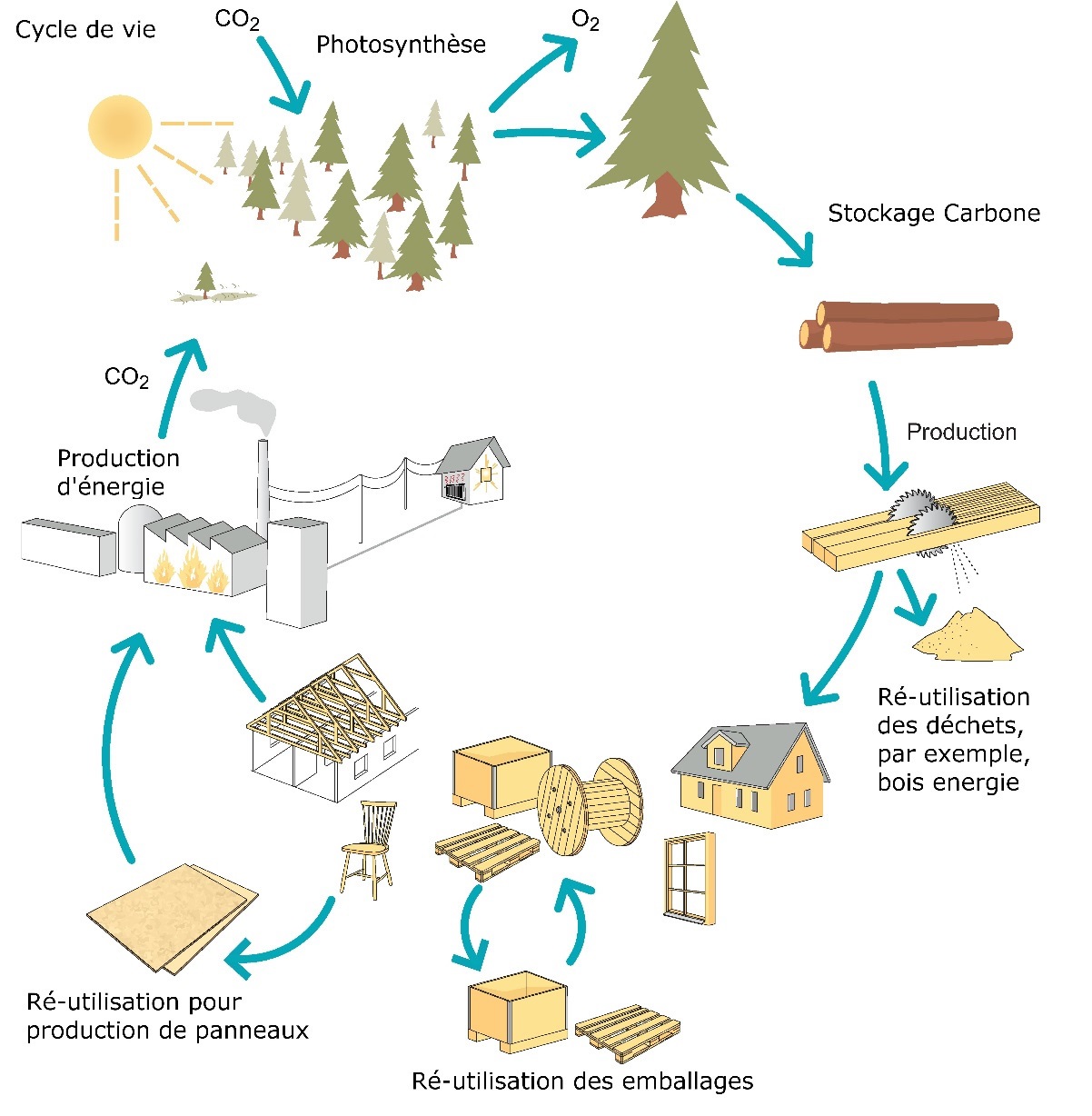
Figure 1.6 : Le cycle de vie des produits du bois : depuis la forêt jusqu’au recyclage
1.4.2. Fabrication raisonnée
Les méthodes utilisées pour fabriquer le bois lamellé présentent d’autres avantages environnementaux. Le bois lamellé est fabriqué à partir de lamelles en bois collées les unes aux autres. Elles n’ont aucun impact négatif sur l’environnement pendant leur cycle de vie et peuvent être facilement utilisées, recyclées ou servir à produire de l’énergie. Les matières utilisées sont le bois (épicéa le plus couramment, mais aussi sapin, pin sylvestre, douglas, mélèze ou encore chêne, western hemlock, pin laricio, pin noir d’Autriche, pin maritime, peuplier, pin radiata, épicéa de Sitka ou western red cedar) et une colle synthétique.
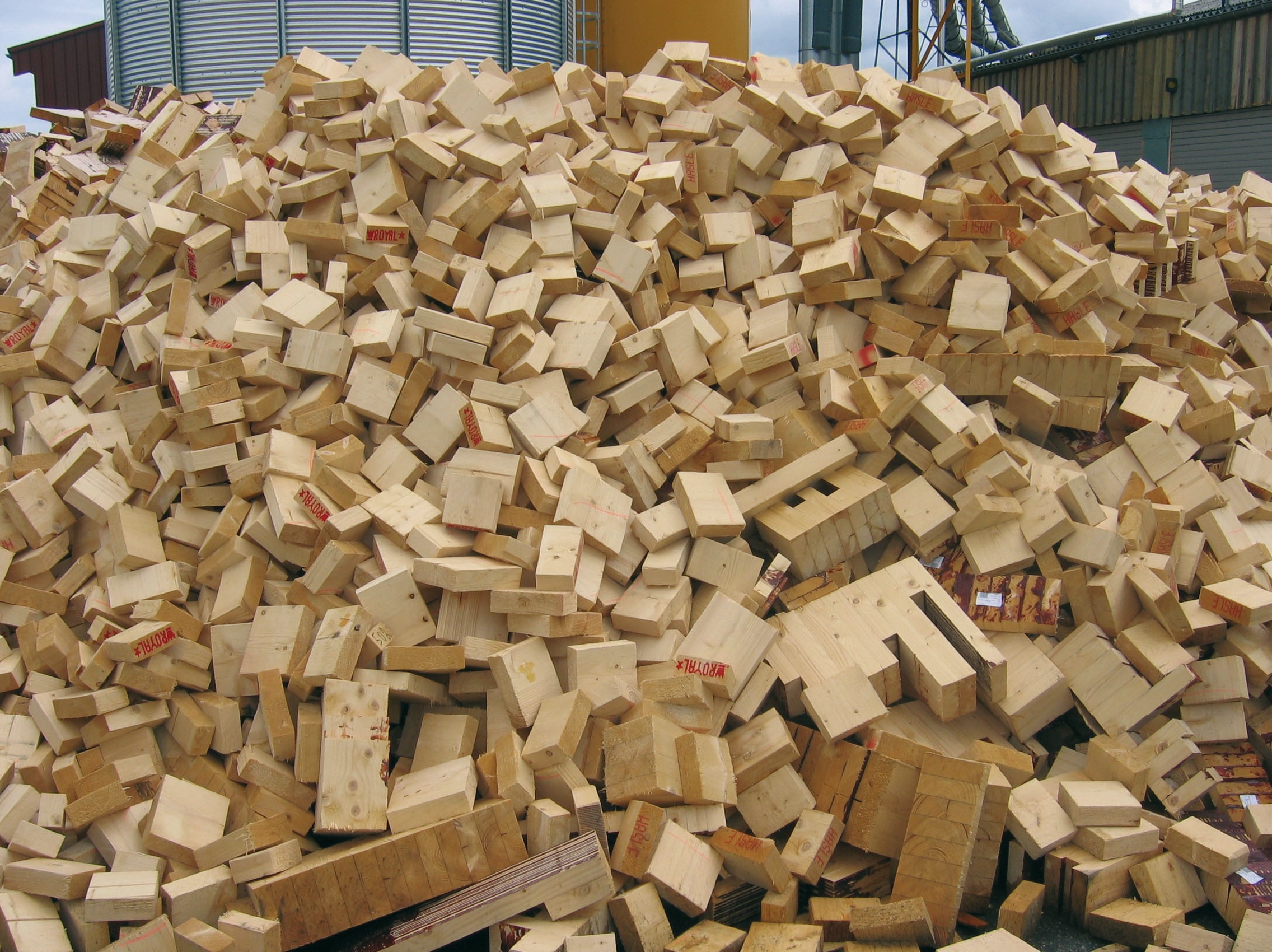
Figure 1.7 : Récupération des chutes de bois lors de la fabrication pour valorisation énergétique.
La colle est fabriquée à partir de matières premières non renouvelables qui se caractérisent par un profil environnemental négatif. La quantité de colle utilisée par unité de volume est cependant si faible (moins de 1% du poids) que l’effet sur le produit final est négligeable. Il est également important de souligner que les colles mises en œuvre ont réalisé des progrès considérables en matière d’émissions (se reporter au Volume 1). Pendant la fabrication, des émissions liées au processus se produisent sous la forme d’eau, utilisée pour nettoyer le matériel d’encollage, l’excès de colle durcie et de petites quantités de matériau inhabituel pendant le durcissement.
Le bois lamellé étant généralement adapté à des projets spécifiques, donnant lieu à une fabrication sur-mesure, il ne génère pas de déchets importants sur le lieu de construction et se distingue ainsi par des chantiers peu polluants présentant un minimum de déchets. Les emballages sont composés de matières recyclables.
Tout au long de son cycle de vie, le bois lamellé n’a aucun impact négatif d’importance sur l’environnement. Lors de sa vie en œuvre, il peut être entretenu selon des méthodes traditionnelles. Il est facilement réparable – les différentes parties d’un élément en bois lamellé peuvent, au besoin, être facilement remplacées. Le bois lamellé peut aussi être travaillé ultérieurement de différentes façons, et notamment par un traitement abrasif ou par ponçage.
Les fabricants de bois lamellé produisent des déclarations environnementales selon un modèle commun (FDES et DEP). Ces déclarations indiquent l’impact environnemental du produit pendant la partie de son cycle de vie pouvant être contrôlée par le fabricant, c’està-dire de l’extraction de la matière première au moment où le produit fini sort de l’usine.
1.5. PRODUCTION DU BOIS LAMELLE COLLE
L’expression « bois lamellé collé » utilisée ci-après est employée dans le même sens que celui défini dans la norme européenne EN 14080, ce qui signifie par ailleurs que toutes les exigences relatives à la fabrication et au produit, énoncées dans ladite norme, sont respectées. Le bois lamellé collé est donc un élément de construction qui se compose d’au moins deux panneaux ou planches de bois (conifère) collés. L’épaisseur des lamelles est au minimum de 6 mm et peut atteindre jusqu’à 45 mm. Le sens du fil doit coïncider avec l’axe longitudinal de l’élément. Les plans de joint sont parallèles à la largeur (normalement la plus petite face de la poutre).
1.5.1. Processus de fabrication
La fabrication du bois lamellé-collé suit globalement les mêmes étapes quel que soit le fabricant ou le pays. La figure ci-dessous donne une représentation schématique du processus de fabrication.
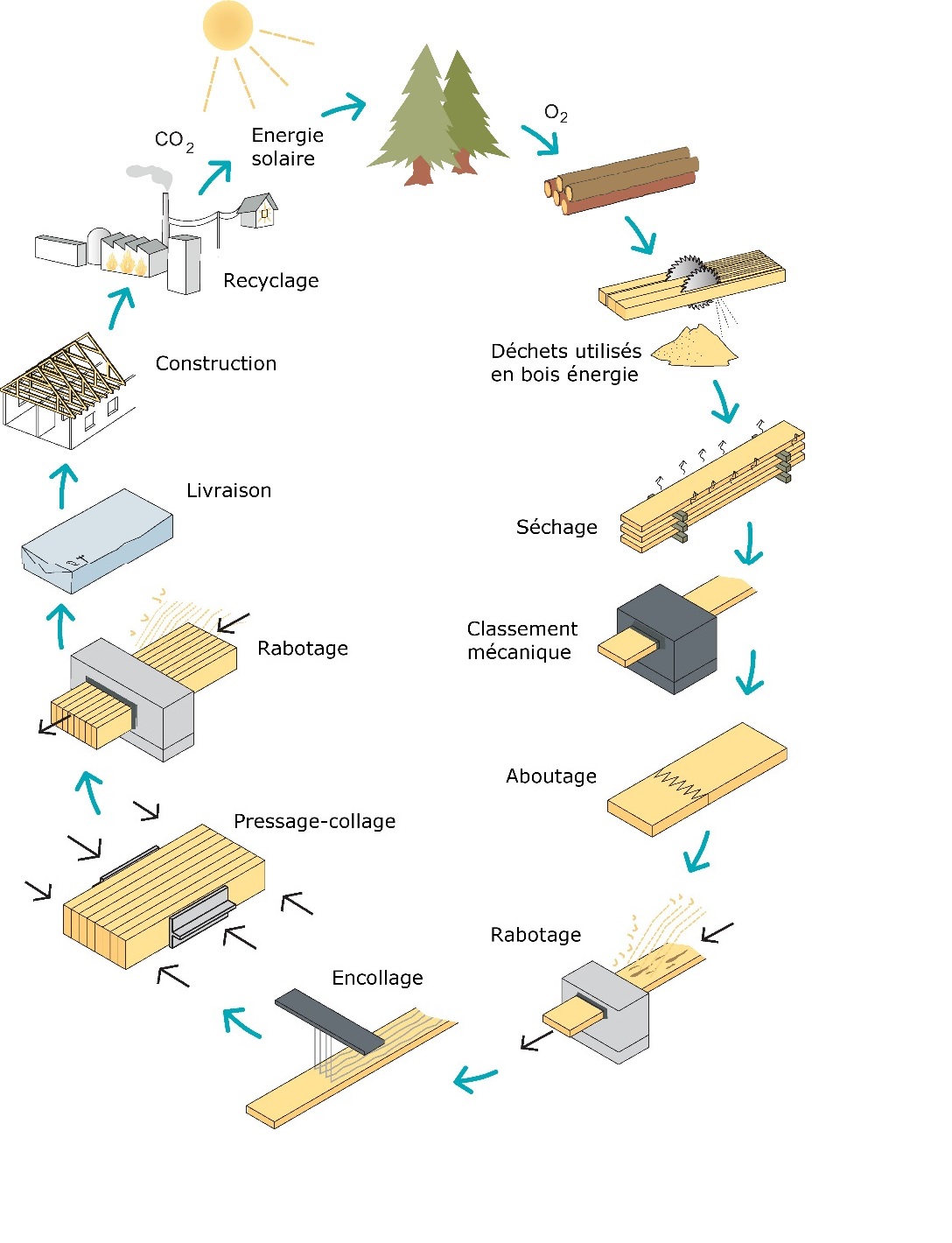
Figure 1.8 : Fabrication du bois lamellé-collé. Représentation schématique.
La matière première utilisée est le bois massif, classé selon sa résistance ; le bois utilisé est généralement de l’épicéa. Pour les travaux de construction destinés à être exposés à des conditions de forte humidité, du pin imprégné (traité sous pression) est parfois utilisé. Dans de rares cas, lorsque des raisons esthétiques imposent d’autres essences de bois, du bouleau ou du mélèze, par exemple, sont utilisés.
En règle générale, le bois qui sort de la scierie est sec et classé selon sa résistance. La teneur en humidité des lamelles doit être comprise entre 6 et 15 % lorsqu’elles sont collées les unes aux autres, et la différence de teneur en humidité entre deux lamelles adjacentes ne doit pas excéder 5 %. La résistance du plan de collage est alors optimale et la teneur en humidité de la structure finie est équilibrée, ce qui réduit le risque de fendage et de déformation. Il est normal que des fissures se forment dans le bois ; elles n’ont généralement pas d’impact négatif sur la capacité résistante de la structure.
La section transversale d’un élément lamellé-collé peut être constituée de lamelles appartenant à une même classe de résistance. Le bois lamellé-collé est alors « homogène ». Néanmoins, les lamelles externes de la section transversale d’une poutre, qui subissent en général les plus fortes contraintes, sont habituellement constituées de bois de meilleure qualité ; ce type de composition est appelé « bois lamellé-collé panaché ». Il est donc nécessaire de prévoir un espace suffisant au sein de l’usine pour stocker simultanément du bois appartenant à au moins deux classes de résistance différentes.
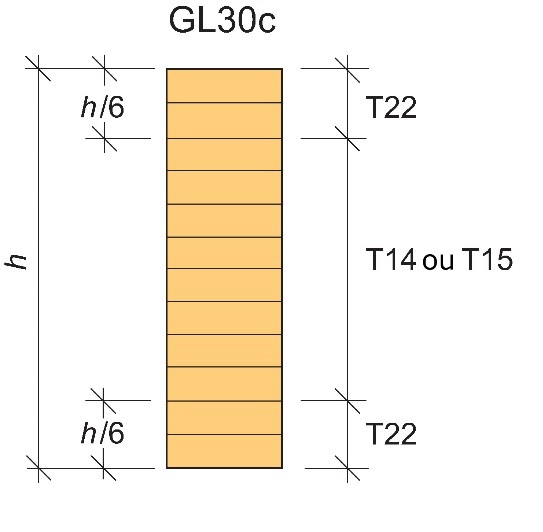
Figure 1.9 : Assemblage de bois lamellé-collé panaché. Exemple d’assemblage possible pour du lamellé-collé classé GL30C conformément à la norme EN 14080. Les notations T14, T15 et T22 correspondent aux classes de résistance ; les nombres correspondant à la valeur caractéristique de la résistance à la traction des lamelles. Les lamelles internes sont classées T14 ou T15. La qualité T14 satisfait des exigences légèrement plus élevées concernant la résistance des aboutages à entures multiples des lamelles externes que la qualité T15.
Les lamelles sont aboutées par entures multiples pour obtenir des lamelles longues (30- 40 m environ). Ces lamelles sont ensuite coupées à la longueur souhaitée et placées les unes sur les autres. Dans le cas du bois lamellé-collé panaché, il convient de faire attention au placement des lamelles internes et externes. Pour empêcher l’apparition de contraintes lors du séchage et du mouillage de la section, les lamelles sont tournées de façon à ce que leur cœur soit orienté dans la même direction dans l’ensemble de la section. Les lamelles externes sont cependant toujours tournées le cœur vers l’extérieur.
Selon le système d’encollage utilisé, il convient de laisser la colle durcir au niveau des aboutages jusqu’à plusieurs heures avant de raboter, puis d’encoller immédiatement, les côtés plats des lamelles.
Les lamelles empilées sont ensuite hissées dans des presses où la pression nécessaire est appliquée. Cette opération doit être réalisée avant que la colle durcisse, après une heure environ, le temps exact dépendant du type d’adhésif utilisé et de la température de la pièce. Les lamelles peuvent être courbées au moment où la pression est appliquée, ce qui donne des formes cambrées ou courbes. La colle durcit ensuite dans des conditions contrôlées d’humidité et de température, à l’aide, éventuellement, d’un système de chauffage. Les poutres droites peuvent aussi être fabriquées à l’aide d’une presse à haute fréquence en continu.
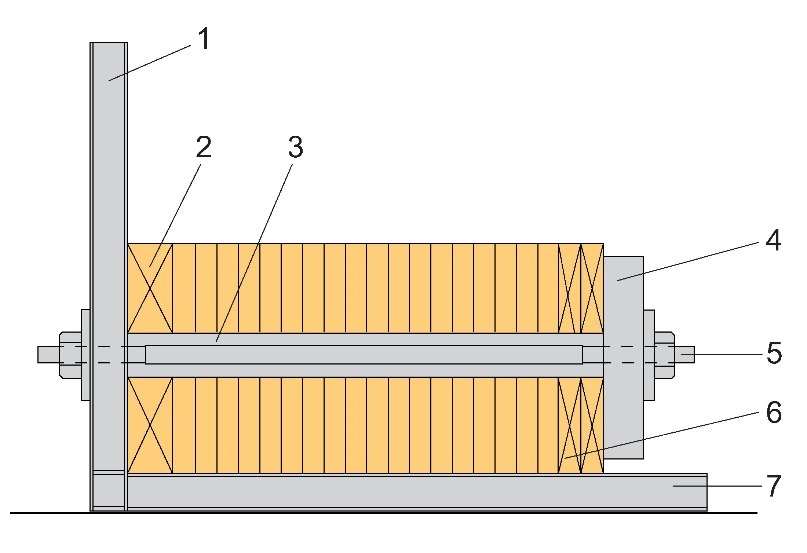
Figure 1.10 : Représentation schématique d’une presse. (1) Butée verticale. (2) Base de répartition de la pression, configuration possible de la contre-flèche. (3) Séparateur. (4) Bloc de compression. (5) Tirant. (6) Planches de répartition de la pression. (7) Butée horizontale.
Lorsque la colle a durci, la pression est relâchée et les éléments lamellés collés sont retirés de la presse pour être placés sur une raboteuse où les côtés sont rabotés selon le degré de finition requis.
Il convient ensuite d’effectuer le travail final, qui consiste par exemple à scier finement les arêtes et à usiner l’élément, notamment pour les assemblages. Dans certains cas, les éléments reçoivent une finition de surface au sein de l’usine. Pour finir, les éléments font l’objet d’une vérification visuelle et d’un marquage avant d’être emballés et chargés en vue de leur transport vers le lieu de construction ou de stockage des produits finis.
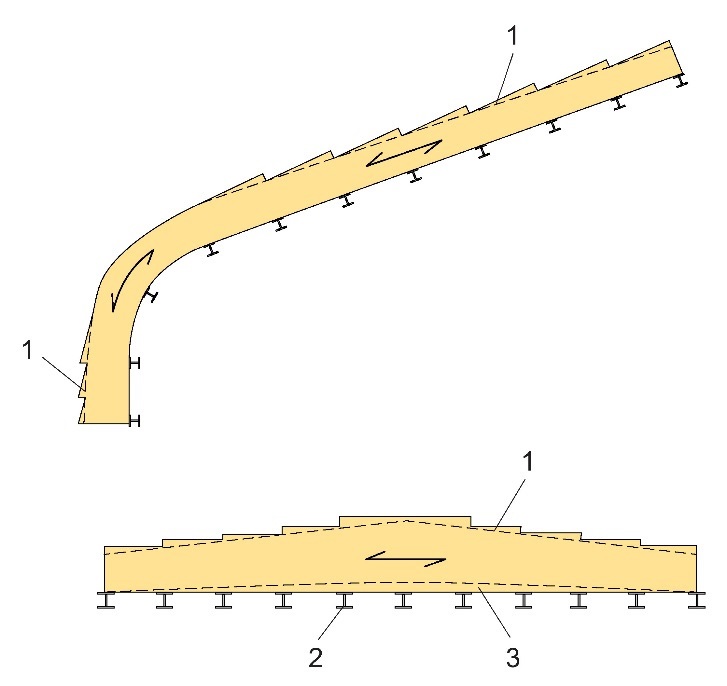
Figure 1.11 : Élément structural à hauteur variable. (1) Dégauchissage. (2) Butée verticale. (3) Base de répartition de la pression, gabarit de la possible contre-flèche.
La fabrication est supervisée par le contrôleur de l’usine qui enregistre les conditions déterminantes pour la qualité des produits, telles que la teneur en humidité du bois lamellé, la température et la teneur en humidité de la pièce où a lieu l’encollage, la durée de l’encollage et du levage.
Le paramètre le plus important dans la fabrication du lamellé-collé est la qualité des plans de collage. Une attention particulière est donc accordée à la résistance des aboutages et à la qualité des plans de collage entre les lamelles par l’intermédiaire d’un contrôle interne permanent de la production en usine. Ce contrôle interne est surveillé par un organisme de contrôle externe agréé par les autorités.
1.5.2. Bois lamellé-collé – marquage CE
La norme européenne EN 14080 et les normes référencées dans la norme EN 14080 définissent les exigences applicables au bois lamellé-collé marqué CE. L’objectif du marquage CE est de permettre la libre circulation des produits sur le marché européen et la comparaison des produits de différents fabricants grâce à la déclaration d’un certain nombre de propriétés (résistance à la flexion, module d’élasticité, réaction au feu, etc.). La norme EN 14080 définit donc les propriétés que doit déclarer le fabricant, les principes généraux à appliquer lors de la fabrication, les exigences relatives aux matières premières et aux équipements et les exigences relatives au produit fini. Afin de respecter les spécifications de la norme EN 14080, le fabricant doit établir, documenter et utiliser un système de contrôle de la production en usine (système CPU) pour garantir que les produits mis sur le marché sont conformes aux caractéristiques indiquées.
Le système CPU comprend des procédures, des inspections et des essais et/ou des évaluations ainsi que l’utilisation des résultats pour contrôler les matières premières, les composants, l’équipement, le processus de fabrication et le produit lui-même. Le système CPU adopté par le fabricant doit être documenté de façon systématique sous la forme de protocoles et de procédures écrites.
Avant de mettre un produit sur le marché, des essais de type initiaux (ETI) ainsi qu’une inspection initiale de l’usine et du CPU doivent être réalisés par un organisme notifié externe. L’ETI vise à évaluer le produit afin de garantir sa conformité avec les propriétés devant être indiquées par le fabricant et les exigences générales de la norme EN 14080. L’inspection initiale de l’usine et du CPU vise à garantir que le CPU inclut tous les éléments à prendre en compte et que ces derniers sont mis en place.
Si l’ETI et les inspections initiales révèlent que toutes les exigences sont satisfaites, le fabricant peut apposer le marquage CE sur ses produits. Une surveillance continue du CPU doit néanmoins s’exercer deux fois par an ; cette surveillance prend généralement la forme de visites inopinées. L’objectif de cette surveillance continue est de garantir que le CPU est toujours assuré et adapté à la production en cours. Tous les éventuels changements de production, par exemple, doivent être évalués ; des inspections relatives à l’entretien des équipements et des outils doivent être effectuées, et les valeurs des essais et des mesures effectués par le fabricant doivent être revues pour garantir qu’elles correspondent toujours aux valeurs des échantillons soumis à l’essai de type initial.
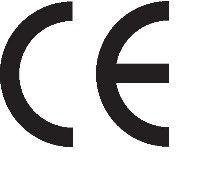
Figure 1.12 : Marquage CE.
1.5.3. Bois massif reconstitué
Le bois massif reconstitué est constitué de 2 à 5 lamelles d’une épaisseur comprise entre 45 et 85 mm ; ce type de bois est également régi par la norme EN 14080. Le bois massif reconstitué possède les mêmes caractéristiques que le bois lamellé-collé, si ce n’est que sa résistance est légèrement plus faible.
1.5.4. Résistance et rigidité
Le bois lamellé-collé possède les mêmes caractéristiques de résistance que le bois de construction ordinaire :
› Sa résistance varie selon l’angle entre la charge et le sens du fil (anisotropie),
› Sa résistance diminue lorsque la teneur en humidité augmente,
› Sa résistance diminue lorsque la durée de charge augmente,
› Les caractéristiques des matériaux sont variables, aussi bien au sein d’un même élément qu’entre différents éléments.
Un élément lamellé-collé se caractérise néanmoins par une résistance moyenne plus élevée et des propriétés de résistance moins variables qu’un élément similaire en bois massif. Cet effet dit de lamellation s’explique généralement de la façon décrite ci-après.
La résistance de la section la plus faible – présence d’un nœud ou aboutage, par exemple – est déterminante pour la résistance d’une planche en bois. Il existe ainsi une différence notable entre les planches. Une poutre en bois lamellé collé se compose cependant de lamelles de différentes résistances et le risque que plusieurs lamelles comportant des défauts majeurs se retrouvent dans la même section de poutre est minime.
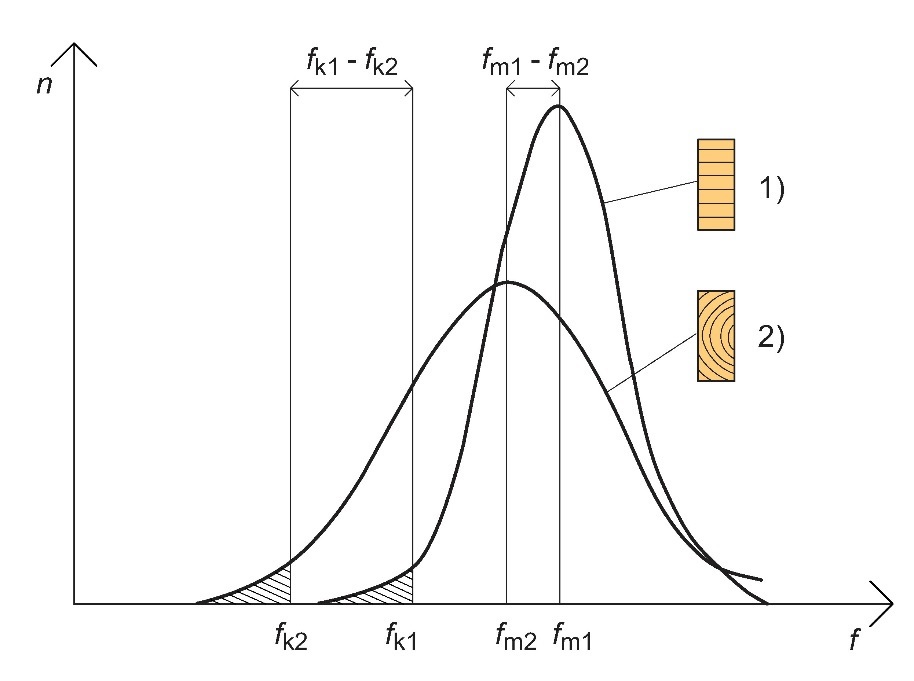
Figure 1.13 : Un élément structural en bois lamellé-collé se caractérise par une résistance moyenne plus élevée et des propriétés de résistance moins variables qu’un élément équivalent en bois massif.
Dans le cas des poutres en bois lamellé collé testées dans des conditions de laboratoire, c’est-à-dire avec une sollicitation à court terme et une teneur en humidité de 12 % environ, les ruptures sont très fragiles et sont presque toujours dues à un nœud ou à un aboutage sur le côté tendu de la poutre. L’écrasement du bois sur le côté comprimé précède parfois la rupture finale, sans pour autant modifier sa nature fragile. Une rupture fragile signifie notamment que la contrainte n’est pas redistribuée pendant le processus de rupture et que la capacité résistante est atteinte lorsqu’à un moment donné, la contrainte dépasse une valeur critique. Étant donné que la probabilité qu’une poutre contienne un défaut capable de provoquer une rupture augmente proportionnellement au volume, la résistance des poutres de grande taille est généralement inférieure à celle des poutres de petite taille. Cet « effet de volume » (effet d’échelle ou loi de Weibull) a été assez bien démontré par des essais à court terme en laboratoire, mais il n’a fait l’objet que d’études incomplètes dans le cas de sollicitations à long terme.
Selon l’Eurocode 5, par exemple, les résistances caractéristiques du bois lamellé-collé sont à la base de la conception. Ces valeurs caractéristiques correspondent aux valeurs formelles d’un grand nombre d’éléments, tels que les poutres lamellées-collées. L’estimation de la résistance caractéristique, par exemple, se base sur l’utilisation d’un diagramme de fréquence pour la résistance à la rupture. À partir de ces données d’essai, il est ensuite possible, avec un degré de précision acceptable, d’adapter une distribution statistique – normale ou log-normale – au diagramme de fréquence ou, au moins, à sa partie centrale.
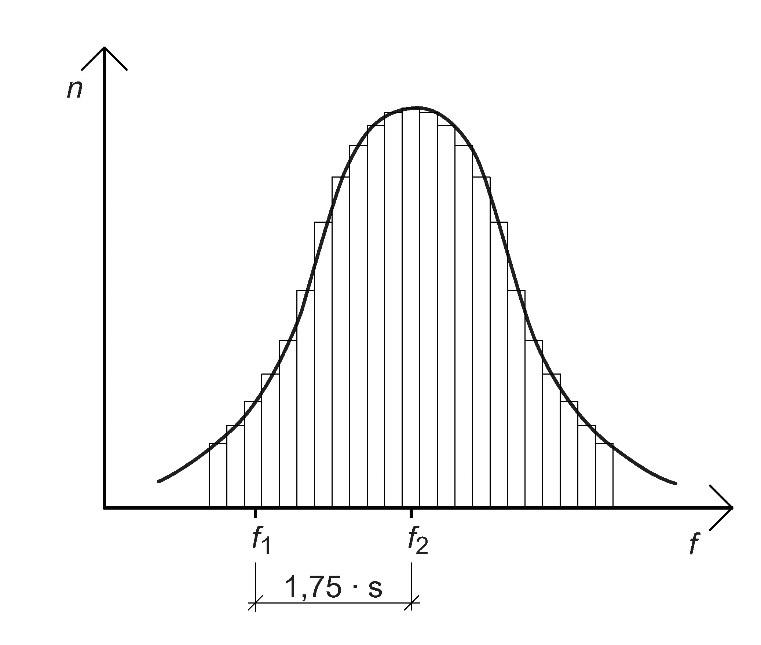
Figure 1.14 : Exemple d’un diagramme de fréquence avec courbe de distribution normale superposée.
Si l’on part du principe, pour simplifier, que la résistance à la rupture est normalement distribuée, il est possible de calculer la valeur caractéristique fk à partir de la formule suivante :
fk = fmean – c.s (1.1)
où
fmean correspond à la moyenne et s à l’écart-type de la résistance. Le paramètre c est un coefficient dont la valeur dépend de la façon dont la valeur caractéristique est définie (c’est-à-dire quel centile), du nombre de points de données utilisés dans l’estimation de la distribution statistique et de l’écart-type utilisé pour le calcul (connu ou estimé). L’écart-type est une mesure statistique de la variabilité des valeurs mesurées. La résistance caractéristique du matériau ne dépend donc pas seulement de la valeur moyenne, mais aussi dans une large mesure de la variabilité du matériau et du nombre d’essais effectués. Dans les situations de calcul structural, la valeur de résistance à utiliser est basée sur la valeur correspondant au fractile à 5 % le plus bas, c’est-à-dire sur la valeur en dessous de laquelle, statistiquement, 5 valeurs réelles sur 100 céderont. Si le nombre d’essais est important, c = 1,75.
Pour les analyses de la déformation à l’état limite de service (module d’élasticité, module de cisaillement), la rigidité est calculée de la même manière, mais en utilisant comme point de départ la moyenne, et non la valeur correspondant au fractile à 5 %. Pour calculer les valeurs de rigidité à utiliser dans les analyses de la résistance – flambement élastique, déversement, par exemple –, la valeur correspondant au fractile à 5 % est utilisée.
1.5.5. Classes de résistance
Une classe de résistance est attribuée au bois lamellé-collé fabriqué conformément à la norme EN 14080. La norme EN 14080 donne la possibilité d’attribuer une classe de résistance au bois lamellé-collé selon différentes méthodes :
a) Calcul des propriétés du bois lamellé-collé en fonction des propriétés des lamelles,
b) Essais sur des poutres en dimensions réelles,
c) Attribution directe d’une classe de résistance conformément à la norme EN 14080.
En règle générale, la résistance d’un élément lamellé-collé est déterminée par la résistance du bois utilisé, sa position dans la section et la résistance des aboutages. La norme EN 14080 prédéfinit un certain nombre de classes de résistance pour le bois lamellé-collé, mais le fabricant peut se servir des méthodes a) et b) précédemment mentionnées pour définir une classe de résistance unique afin, par exemple, d’optimiser le rendement de la matière première localement disponible. Le Tableau 1.1 et le Tableau 1.2 indiquent les valeurs de résistance et de rigidité pour les classes de résistance du bois lamellé-collé prédéfinies dans la norme EN 14080. Le Tableau 1.3 fournit les équations à utiliser pour définir un profil de résistance unique.
Tableau 1.1 : Classes de résistance du bois lamellé-collé définies dans la norme EN 14080. Bois lamellé-collé panaché. Le fabricant peut également définir une classe de résistance unique afin de maximiser le rendement de la matière disponible.
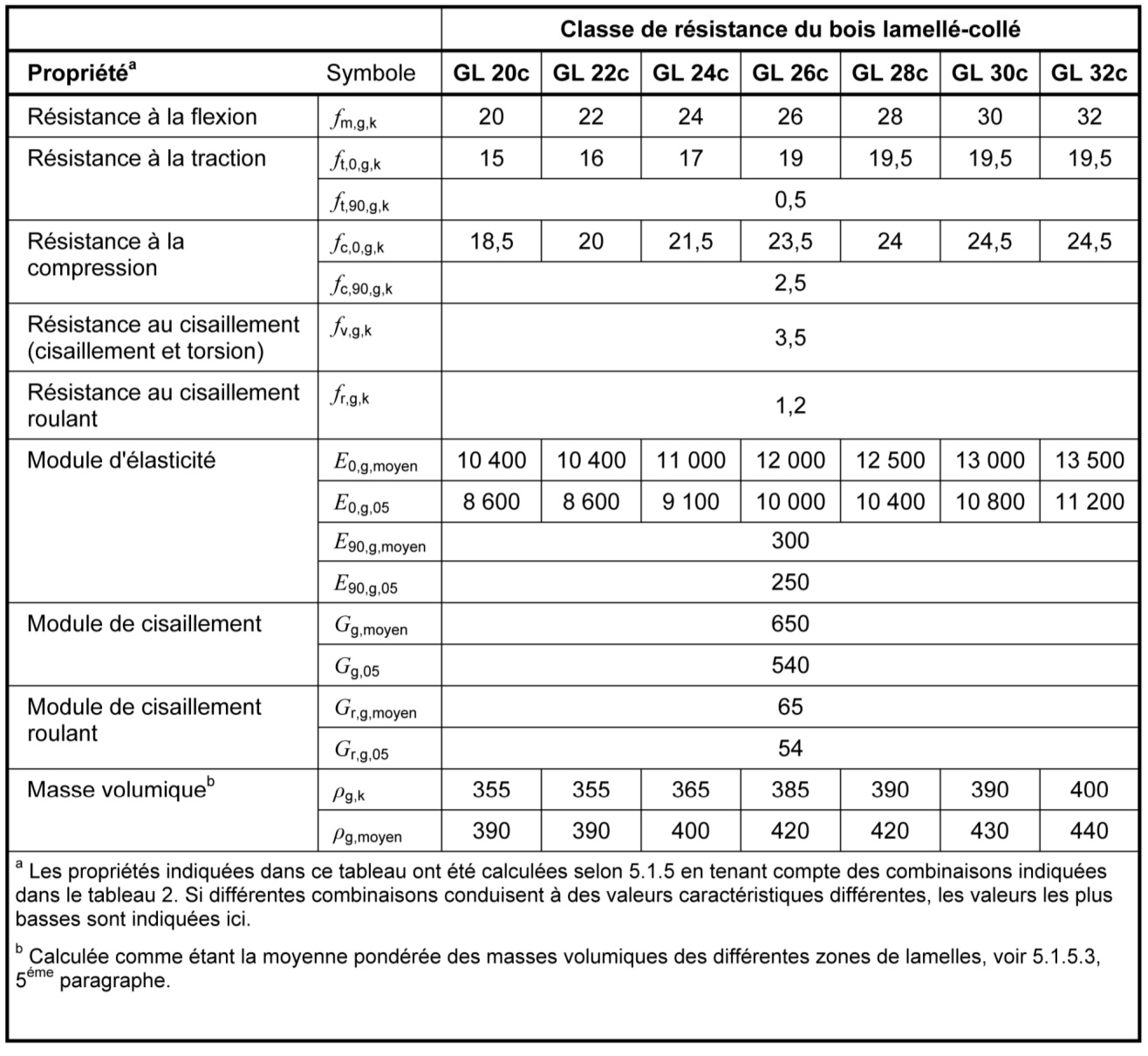
Tableau 1.2 : Classes de résistance du bois lamellé-collé définies dans la norme EN 14080. Bois lamellé-collé homogène. Le fabricant peut également définir une classe de résistance unique afin de maximiser le rendement de la matière première disponible.
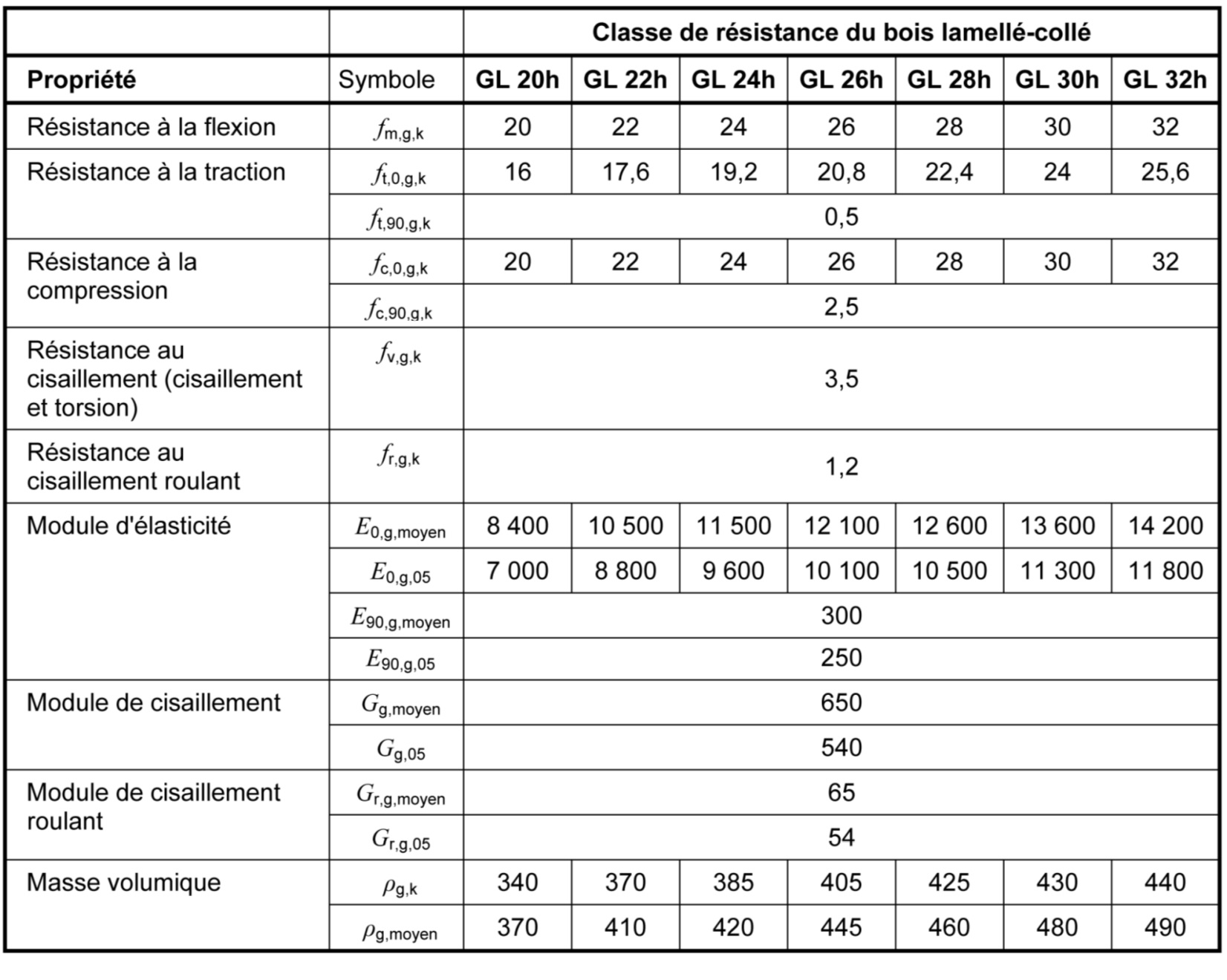
Tableau 1.3 : Résistances caractéristiques et rigidités en N/mm² et masses volumiques en kg/m3 du bois lamellé-collé homogène.
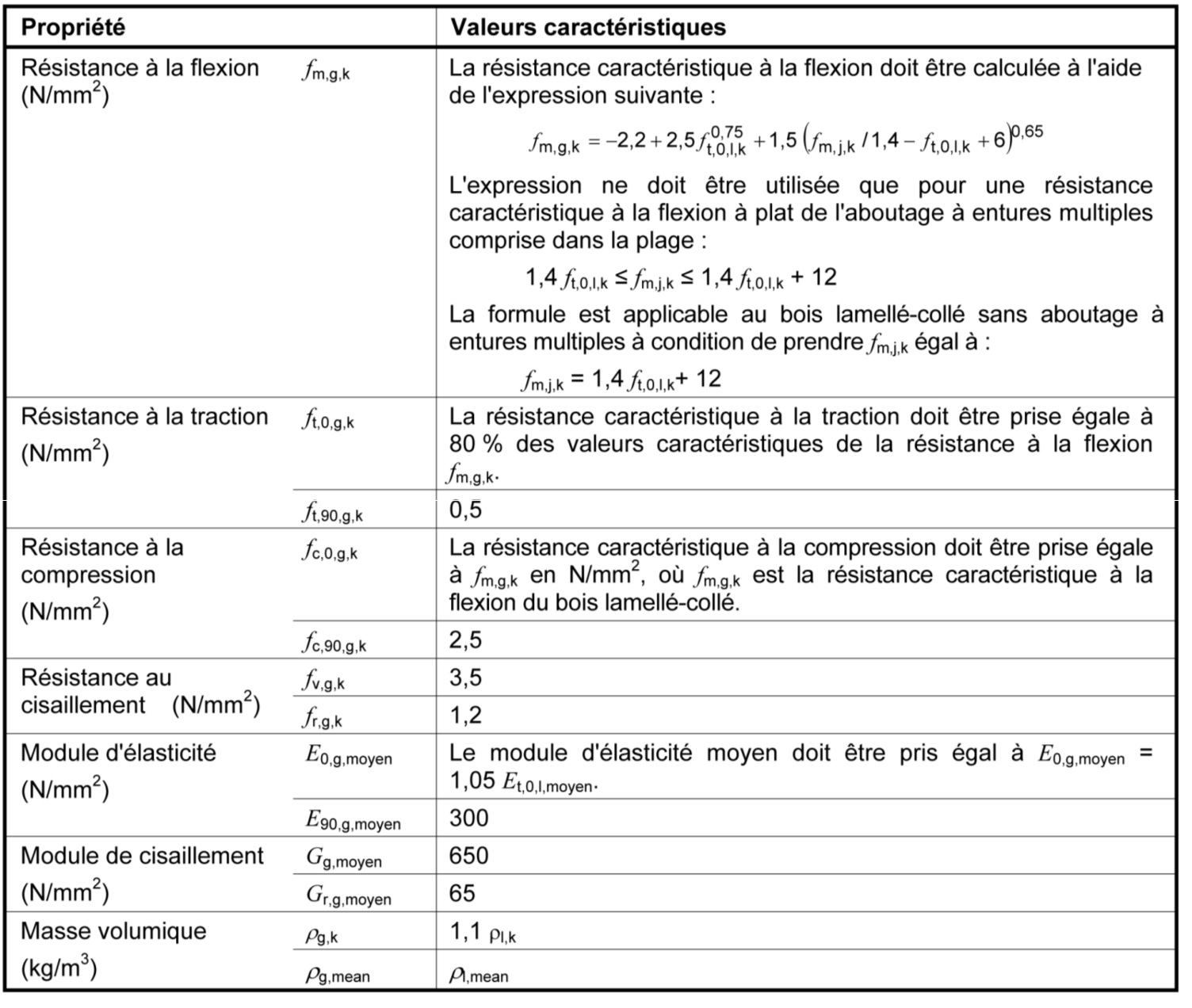
Il convient de noter que ni l’Eurocode 5 ni la norme EN14080 n’indiquent de valeurs de résistance ou de rigidité pour les éléments en flexion selon l’axe faible, c’est-à-dire en flexion selon un axe perpendiculaire aux plans de collage de la section. Ceci est problématique en cas de flexion oblique.
Une solution simple consiste à utiliser la même résistance pour la flexion selon l’axe y et la flexion selon l’axe z, c’est-à-dire que fm,y,d = fm,z,d.
1.5.6. Bois lamellé-collé refendu
Le bois lamellé-collé peut être scié perpendiculairement aux plans de collage en 2 ou 3 parties (bois lamellé-collé refendu).
Il convient de noter que le bois lamellé-collé refendu fait l’objet d’un traitement spécial dans la norme EN 14080. Les poutres lamellées-collées étroites, dont la largeur est inférieure à 90 mm, sont généralement fabriquées en sciant des sections plus larges à l’aide d’une scie à ruban. La norme EN 14080 définit des règles concernant le déclassement possible du bois lamellé-collé en conséquence de cette procédure de refend. Conformément à la norme EN 14080, chaque partie doit avoir une largeur minimum b de 38 mm et un rapport hauteur/largeur maximum de h/b ≤ 8. Selon la procédure de classement et l’assemblage, la résistance caractéristique du bois lamellécollé refendu doit être déterminée à l’aide de la méthode a) ou b) comme suit :
a) Si la procédure de classement garantit que toutes les lamelles de l’élément lamellé-collé refendu possèdent les propriétés déclarées, la résistance, la rigidité et la masse volumique du bois lamellé-collé refendu doivent être déterminées en fonction des propriétés des lamelles.
b) Si les deux exigences décrites ci-après sont respectées, la valeur caractéristique de la résistance à la flexion fm,s,k du bois lamellé-collé refendu en flexion doit être déterminée à partir de la valeur caractéristique de la résistance à la flexion fm,g,k du bois lamellé-collé en vraie grandeur par l’équation (1.2) ou (1.3) :
i. la valeur caractéristique de la résistance à la traction de la lamelle est, au minimum, de 18 N/mm² et, au maximum, de 30 N/mm² et
ii. la valeur caractéristique de la résistance à la traction des lamelles internes n’est pas inférieure de plus de 8 N/mm² à la valeur caractéristique de la résistance à la traction des lamelles externes.
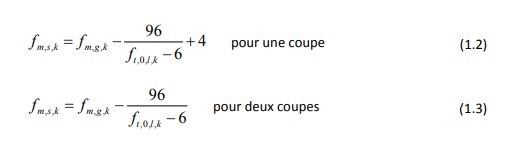
où :
fm,s,k correspond à la valeur caractéristique de la résistance à la flexion du bois lamellé-collé refendu en N/mm² ;
fm,g,k correspond à la valeur caractéristique de la résistance à la flexion du bois lamellécollé avant d’être refendu en N/mm² ;
ft,0,l,k correspond à la valeur caractéristique de la résistance à la traction des lamelles externes en N/mm².
La valeur moyenne du module d’élasticité parallèle au fil E0,s,mean du bois lamellé-collé refendu doit être déterminée à partir de la valeur moyenne du module d’élasticité E0,g,mean du bois lamellé-collé en vraie grandeur par l’équation (1.4) :

Les autres propriétés mécaniques doivent être déterminées à l’aide du Tableau 1.3. Les valeurs de la masse volumique sont les mêmes que celles du bois lamellé-collé en vraie grandeur.
Toutefois, si la procédure de classement utilisée pour classer les lamelles garantit également les propriétés des lamelles refendues, aucun déclassement n’a lieu d’être.
1.5.7. Adhésifs
Les adhésifs utilisés possèdent des propriétés reconnues en termes de résistance et de durabilité en cas de sollicitation à long terme. Seuls sont utilisés des adhésifs justifiant d’une longue expérience pratique. Les exigences formelles relatives aux adhésifs sont définies dans les normes EN 14080, EN 301 et EN 302.
Auparavant, les adhésifs utilisés pour fabriquer le bois lamellé-collé étaient généralement des adhésifs bi composants synthétiques du type phénol-résorcinol-formaldéhyde (PRF). Tous les adhésifs PRF qui servent à fabriquer le bois lamellé-collé sont de type I et peuvent être utilisés quelle que soit la classe de service, c’est-à-dire aussi bien à l’intérieur qu’à l’extérieur. Les adhésifs PRF produisent des joints brun-rougeâtre sombres.
À l’heure actuelle, les adhésifs les plus courants sont les colles MUF (mélamine-uréeformaldéhyde). Ce type d’adhésif procure également une adhérence résistante et durable, adaptée à toutes les classes de service. Les joints fraîchement enduits de mélamine sont clairs, mais s’assombrissent au fil du temps.
Pour l’aboutage à entures multiples des lamelles, le choix porte généralement sur la mélamine la plus claire. Le marquage du bois lamellé-collé doit indiquer le type de colle utilisée (I ou II conformément à la norme EN 14080).
Les adhésifs font l’objet d’un développement continu et de nouveaux types sont régulièrement mis sur le marché. Il est ainsi possible d’utiliser des adhésifs polyuréthane monocomposants (classes de service 1 et 2).
Outre les adhésifs utilisés pour fabriquer le bois lamellé-collé lui-même, des adhésifs servent à la fabrication des assemblages (plaques métalliques et goujons collés) ou pour réparer sur place des structures anciennes. Dans ces cas, les adhésifs polyuréthane ou époxyde sont couramment utilisés.
1.6. ÉLEMENTS LAMELLES-COLLES. DIMENSIONS ET FORMES
La technique du bois lamellé-collé permet de varier la forme de la section transversale, la géométrie et la taille des éléments structuraux. Les limites sont fixées par des aspects pratiques, tels que la taille du lieu de production, la capacité des équipements mécaniques et les possibilités de transport. Certains de ces facteurs limitants sont commentés ci-après.
Les sections rectangulaires sont les plus courantes, mais d’autres sections peuvent être fabriquées, et notamment des sections en forme d’I, de T et de L, des sections creuses ou une combinaison de sections rectangulaires collées en bloc.
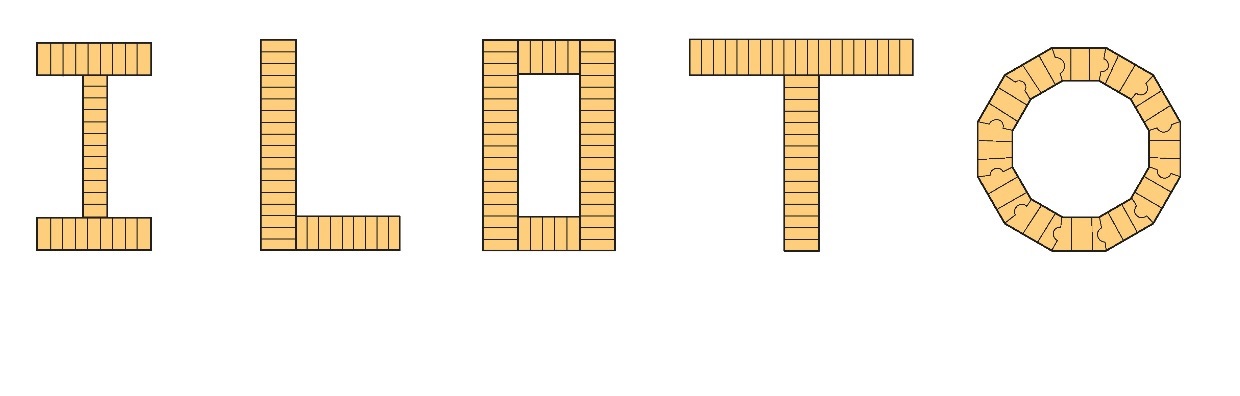
Figure 1.15 : Exemples de sections conçues à partir de sections rectangulaires composées de plusieurs éléments lamelléscollés.
1.6.1. Norme de production – Dimensions standards
Les éléments lamellés collés droits de section rectangulaire sont normalement composés de lamelles (pin traité) de 45 mm ou 33 mm d’épaisseur. Leur largeur correspond aux gammes standards des scieries. Une fois les côtés rabotés (environ 10 mm au total), on obtient des largeurs standards de 90, 115, 140, 165, 190, 215 et 240 mm. L’exactitude des dimensions dépend du traitement des côtés, à savoir s’ils sont destinés à être rabotés et poncés ou seulement rabotés, auquel cas il est toléré que les côtés ne soient pas complètement rabotés.
Le Tableau 1.4 donne les dimensions usuelles. Les dimensions sont valables pour les éléments dont la surface est proprement rabotée à une teneur en humidité de référence de 12 %. Les éléments courbes peuvent – selon le rayon – nécessiter des lamelles plus fines.
Tableau 1.4 : Sections transversales des éléments lamellés collés droits. Dimensions nominales correspondant aux surfaces rabotées (mm). Dimensions standards usuelles.
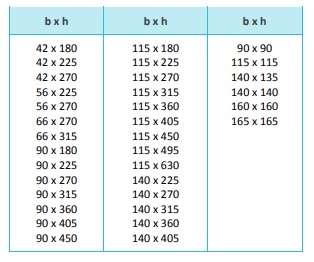
1.6.2. Dimensions maximales de la section
La largeur maximale (mesurée parallèlement au plan de collage) est limitée par le simple fait qu’il est difficile d’obtenir du bois de sciage d’une largeur supérieure à 225 mm ; dans certains cas, toutefois, il est possible de se procurer du bois dont la largeur peut atteindre jusqu’à 260 mm. Après rabotage, cela équivaut respectivement à des largeurs nominales de 215 mm et 240 mm. Il est possible de concevoir des éléments mesurant jusqu’à 700- 800 mm de large (190 + 190 + 190 + 190 = 760 mm) en les collant en bloc. Il est également possible d’obtenir des poutres d’une grande largeur en encollant les chants des lamelles avant de former la section transversale.
La hauteur maximale (dimension de la section mesurée perpendiculairement au plan de collage) est limitée à environ 2 m par les machines à raboter. Plusieurs méthodes permettent d’obtenir de plus grandes hauteurs, et notamment l’encollage du faîtage d’une poutre à double décroissance à un stade ultérieur, après le rabotage. Il a ainsi été possible de concevoir des poutres lamellées-collées mesurant jusqu’à 3 m de haut.
L’utilisation judicieuse du matériau implique souvent des poutres hautes et étroites, qui sont parfois difficiles à manipuler sur le lieu de construction. Pour des raisons pratiques, la largeur ne doit pas être inférieure à 1/10 de la hauteur.
1.6.3. Longueur maximale
Certaines usines de bois lamellé-collé produisent des éléments pouvant mesurer jusqu’à 40 m de long. Dans la pratique néanmoins, la longueur est restreinte par les infrastructures de transport.
1.6.4. Contre-flèche
Il est parfois nécessaire de courber les poutres lamellées-collées en appui simple à grande portée (plus de 10-12 m) afin de réduire les problèmes dus aux flèches. Il est possible de concevoir une poutre avec une contre-flèche moyenne mesurant jusqu’à 200 mm. Des recommandations concernant l’ampleur de la contre-flèche sont données dans cet ouvrage.
1.6.5. Déviations autorisées
Les éléments lamellés collés sont fabriqués avec autant de précision que les sections en acier laminé ou les éléments en béton. Les déviations autorisées sont indiquées dans la norme EN 14080. Le tableau ci-dessous présente plusieurs déviations autorisées de base.
Tableau 1.5 : Déviations autorisées pour le bois lamellé-collé.
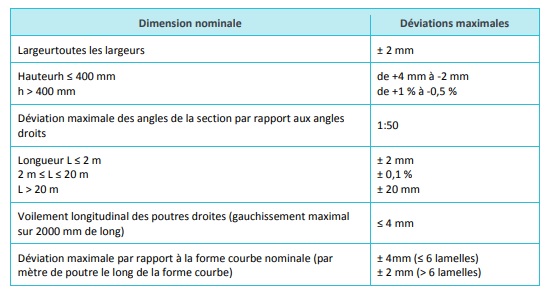
1.7. ASPECT ET FINITION DE SURFACE
Le bois lamellé-collé est un matériau de construction dont les principales qualités sont en principe la résistance, la rigidité et la durabilité.
Les éléments lamellés collés ne possèdent généralement pas la qualité d’aspect et la finition de surface exigées pour les ouvrages de menuiserie et le mobilier. La plupart des produits standards respectent néanmoins des exigences normales en matière d’aspect, pour autant qu’ils soient convenablement traités lors du transport et sur le lieu de construction.
1.7.1. Bois
Le lamellé-collé est fabriqué à partir de bois classé selon sa résistance, ce qui signifie qu’il contient des nœuds de taille réduite, mais non qu’il en est dépourvu. Le bois à haute résistance peut également contenir des nœuds assez importants – dans le cas des lamelles du milieu, le diamètre du nœud peut être aussi large que l’épaisseur de la lamelle.
1.7.2. Joints de colle
Comme mentionné ci-dessus, les adhésifs phénol-résorcinol produisent des joints sombres alors que les adhésifs mélamine produisent des joints clairs. Les joints à base de mélamine peuvent cependant s’assombrir au fil du temps. Les aboutages des lamelles apparaissent alors sous la forme de taches sombres ou de fines lignes en zigzag sur les côtés des éléments, en particulier si de la colle phénol-résorcinol a été utilisée.
Les éléments lamellés collés dont la largeur est inférieure à 90 mm sont généralement sciés à partir d’éléments plus larges. Le trait de scie peut alors passer par des fissures ouvertes ou obturées par de la colle, ce qui peut provoquer un éclatement et, en particulier si de la colle phénol-résorcinol a été utilisée, des taches de colle clairement visibles sur la surface sciée. Il convient donc d’éviter d’utiliser des éléments refendus en cas d’exigences élevées en matière d’aspect.
1.7.3. Surfaces
Lorsque les éléments lamellés collés sont retirés de l’encolleuse, ils (les côtés en particulier) sont irréguliers et marqués par l’excédent de colle qui a débordé des joints. Pour des raisons pratiques et esthétiques, les quatre côtés sont donc rabotés avant la livraison. Les exigences du client en matière d’aspect déterminent la quantité à raboter. L’architecte et l’ingénieur en structure doivent se mettre d’accord sur le travail à réaliser dans chaque cas. L’ingénieur en structure peut ensuite concevoir la structure en se servant de la dimension réelle des éléments comme point de départ.
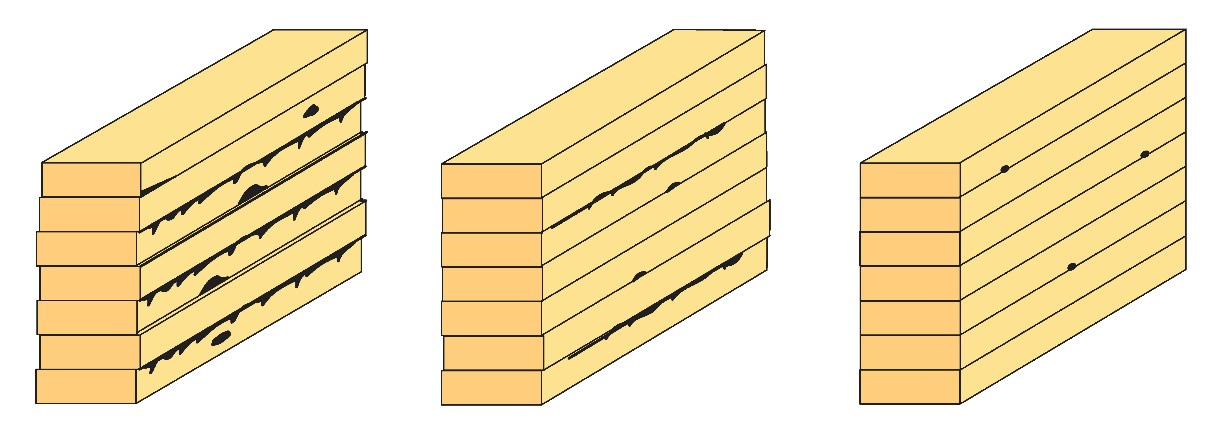
Figure 1.16 : Exemples de catégories d’aspect. De gauche à droite : surfaces égalisées, surfaces rabotées (catégorie d’aspect industrielle) et surfaces proprement rabotées ou surfaces proprement rabotées et réparées (catégorie d’aspect architecturale).
1.7.4. Traitement de surface
L’objectif du traitement de surface est de donner à la surface du bois l’aspect souhaité et de protéger le matériau des changements soudains d’humidité pour empêcher la formation de fissures. Par ailleurs, les finitions qui entraînent la formation d’une pellicule, telles que la peinture ou la laque, permettent de garder plus facilement le bois propre et contribuent à le protéger des dommages mécaniques. Les finitions de surface peuvent aussi être utilisées pour empêcher la propagation des flammes et l’émission de fumées en cas d’incendie.
La surface du bois lamellé-collé peut être traitée suivant les méthodes et à l’aide des produits utilisés pour le bois ordinaire, et donc être teintée, peinte ou laquée. Les exigences techniques, économiques et esthétiques déterminent le choix à prendre dans chaque cas particulier. Les éléments lamellés collés sont fournis non traités, sauf s’il en a été convenu autrement.
Si les exigences en matière d’aspect sont basses, le bois lamellé-collé ne nécessite normalement aucun autre traitement à l’intérieur. La structure doit être protégée par d’autres moyens pendant toute la durée de la construction afin de ne pas être endommagée par l’humidité et d’empêcher l’apparition de taches. Dans le cas des structures situées à l’extérieur mais protégées, il suffit généralement d’utiliser un apprêt
(une teinte incolore ou pigmentée, par exemple), éventuellement combiné à une protection chimique contre les attaques fongiques qui favorisent la décoloration. Si les exigences visuelles sont élevées, il peut être nécessaire d’appliquer un ou plusieurs revêtements.
Le bois lamellé-collé situé à l’extérieur est soumis à une teneur en humidité très variable ; il convient donc de le traiter pour réduire le risque de fendage dangereux. Dans ce cas également, la protection contre l’humidité peut être combinée à une protection chimique du bois. Le traitement de surface ne fournit cependant pas de protection durable contre la pourriture (voir la section ci-après sur la protection du bois). Il convient, lorsque cela est possible, de protéger les structures en bois lamellé-collé situées à l’extérieur en les recouvrant d’un toit ou d’un revêtement aéré.
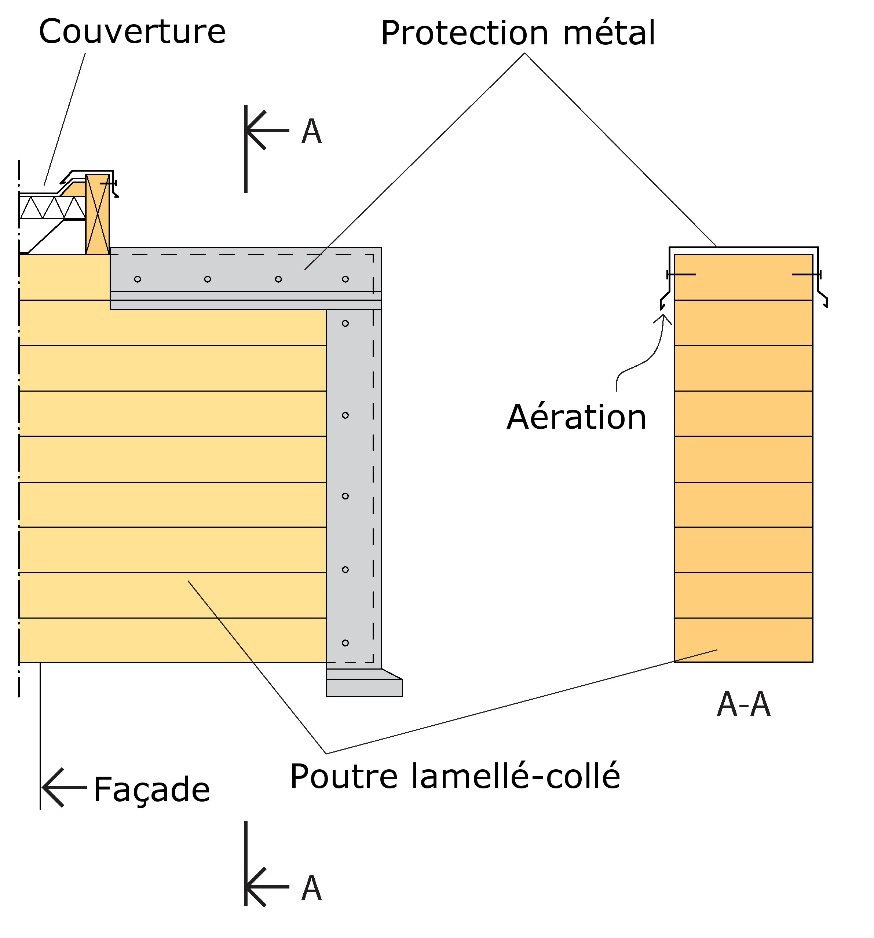
Figure 1.17 : Exemple de protection d’une poutre en porte-à-faux située à l’extérieur.
En l’absence de traitement externe, le matériau vieillit sous l’influence des UV et du mauvais temps et acquiert au fil des années une surface gris velours ou brun goudron en cas d’emplacement ensoleillé. Ces couleurs sont typiques des vieux bâtiments en bois. Il n’existe à l’heure actuelle aucun traitement de surface permettant de préserver sur le long terme et dans des conditions d’entretien raisonnables l’aspect « blanc » du bois frais situé à l’extérieur. Si le vieillissement naturel du bois n’est pas souhaitable dans le cas d’une structure extérieure, il convient de choisir un traitement coloré.
Tous les traitements de surface externes doivent faire l’objet d’un entretien. Le but des opérations d’entretien et les intervalles qui les séparent dépendent de l’emplacement de la structure et du type de traitement de surface choisi. Les teintes nécessitent des opérations d’entretien plus fréquentes que les peintures opaques, mais sont plus faciles à entretenir. Afin que la surface ne s’assombrisse pas à chaque traitement, l’entretien de la surface teintée peut être effectué à l’aide d’une teinte incolore ou diluée.
1.7.5. Protection du bois de construction
Le bois est une matière organique qui peut, dans certaines circonstances, être attaquée par des champignons ou des insectes ravageurs. Dans chaque cas particulier, ceci peut sembler être un désavantage, mais d’un point de vue écologique, il s’agit d’un des principaux avantages de ce matériau. Tout au long de la durée de vie du bâtiment, la structure doit cependant être protégée de ces attaques. Il convient pour ce faire de procéder à une conception rigoureuse des détails pour garantir que les conditions qui président à la décomposition ne se présentent pas.
La protection du bois de construction repose sur le principe de garder le bois aussi sec que possible (teneur en humidité inférieure à 20 %). Si cela n’est pas possible, la structure doit être conçue de façon à sécher rapidement après avoir été mouillée. Lorsqu’il est sec, le bois ne se dégrade pas. Il est très important d’utiliser des accessoires bien conçus pour empêcher la pénétration de l’humidité ; au moment de concevoir les joints et les organes d’assemblage, il convient de veiller à ce que l’eau libre ne puisse pas s’infiltrer dans le bois (en limitant l’exposition des surfaces du bois de bout, en évitant les petits espaces qui entraîneront une succion capillaire, etc.). Dans certains cas (construction d’un pont par exemple), la protection la plus simple consiste à recouvrir complètement le lamellé-collé de panneaux ou de planches de bois. Il est ensuite facile de les remplacer. Lors de la construction d’un pont, il est également courant d’utiliser des passerelles pour piétons couvertes, car elles permettent d’améliorer non seulement le confort des utilisateurs finaux, mais aussi la protection environnementale.
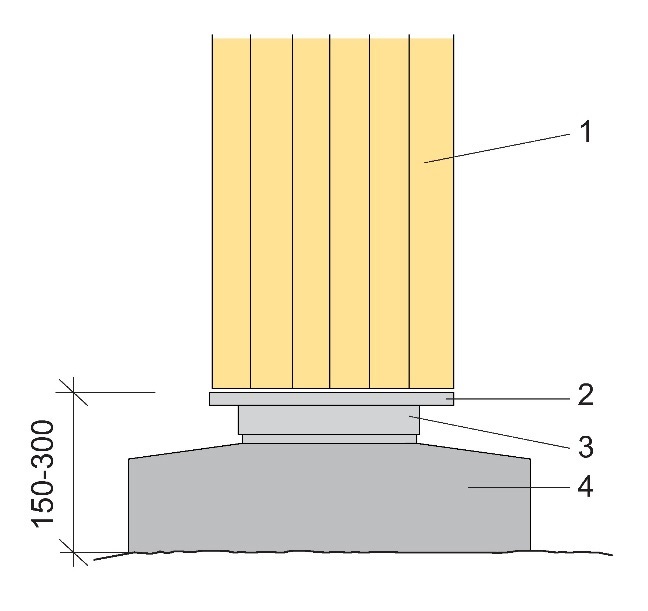
Figure 1.18 : Système de protection du bois pour une base de poteau lamellé-collé. 1. Poteau lamellé-collé. 2. Protection contre l’humidité à l’aide d’un panneau de fibres dures de 5 mm, par exemple. 3. Plaque d’espacement (en acier, bois traité ou béton). 4. Fondation en béton.
Une autre méthode efficace pour protéger le bois de la pourriture consiste à traiter le bois sous pression à l’aide d’un fluide protecteur approprié. Le traitement autoclave ne remplace cependant pas une conception bien détaillée et doit seulement être considéré comme un complément, car la pénétration d’humidité dans la structure cause des problèmes autres que la pourriture.
Le choix du produit de traitement et les exigences relatives à la pénétration et à l’absorption doivent constituer un compromis entre le souhait du propriétaire du bâtiment d’une protection efficace contre la pourriture et les exigences de la société d’un environnement sain et exempt de substances toxiques. L’utilisation d’une protection chimique est réglementée par la législation et diverses normes.
Le bois lamellé-collé peut être fabriqué à partir de lamelles qui ont été traitées avant d’être rabotées et collées. Après le collage, les côtés peuvent soit être laissés bruts ou être rabotés normalement en usine. Dans les deux cas, l’application d’un produit approprié permet d’améliorer l’effet protecteur.
Le bois lamellé-collé peut aussi être traité après le collage, mais la taille de l’élément est alors limitée par la taille de l’équipement nécessaire au traitement. En raison du risque de fendage, le traitement doit être effectué à l’aide de produits à base d’huile. Les produits créosotes doivent être utilisés avec beaucoup de prudence pour assurer la sécurité des travailleurs.
1.8. PROTECTION PENDANT LE TRANSPORT, LE STOCKAGE ET LE MONTAGE
Les éléments lamellés collés destinés à être visibles dans la structure finale sont livrés sous emballage, individuellement ou en lot, dans un film plastique ou du papier afin d’être protégés de la pluie/neige et de la saleté pendant le transport, le stockage et le montage.
L’emballage n’offre pas une protection fiable contre l’humidité. Dans des circonstances défavorables, l’humidité peut en effet se condenser à l’intérieur de l’emballage. L’emballage doit alors être ouvert pour évacuer l’eau. Il est donc préférable dans la plupart des cas de retirer l’emballage des éléments lamellés collés dès que possible après le montage (à condition que la toiture soit en place et que les conditions atmosphériques à l’intérieur du bâtiment soient appropriées). Cela permet de réduire le risque d’apparition de taches d’humidité à la surface du bois lamellé-collé, ce qui doit bien entendu être évité lorsque des surfaces de bois nu restent visibles une fois le bâtiment fini.
Au moment de stocker les éléments lamellés collés sur le lieu de construction, il convient de faire attention à différents aspects :
› Ne jamais poser les éléments lamellés collés directement sur le sol ;
› Placer les éléments sur des supports transversaux propres (!) d’au moins 250 mm de haut qui assurent une bonne ventilation ;
› Le sol doit être sec et plat afin que les éléments ne se déforment pas ou ne soient pas inégalement sollicités ;
› Placer des liteaux transversaux propres (!) entre les éléments et placer les liteaux verticalement l’un sur l’autre.
En cas de stockage en plein air, les éléments lamellés collés doivent être protégés à l’aide de bâches, par exemple, et être placés sur des liteaux propres (!) afin que l’aération soit suffisante sous les bâches. Les bâches ne doivent pas toucher le sol.
Le stockage à long terme des éléments sur le lieu de construction doit être évité, en particulier à l’extérieur.
Il peut être convenu que les éléments lamellés collés soient livrés avec une protection des bords pour réduire le risque d’endommagement pendant le transport et le montage. Lors du levage par grue, il convient d’utiliser des sangles larges et de protéger les bords des éléments lamellés collés à l’aide de cornières en acier ou d’un système similaire afin que le levage ne laisse pas de marques. Les gants de travail, les sangles et tout autre matériel de levage doivent être exempts de salissures non adhérentes. Ne pas marcher sur les surfaces qui seront apparentes une fois le montage terminé !
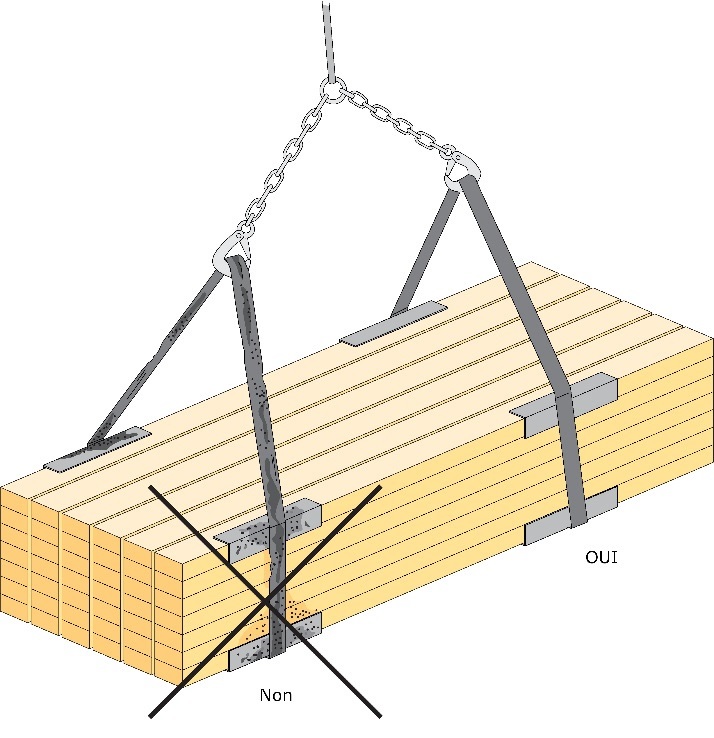
Figure 1.19 : Vérifier que les gants de construction, les sangles et tout autre matériel de levage sont propres.
1.8.1. Transport et montage
Le transport et le montage sont les dernières étapes de la construction d’une structure en bois lamellé-collé. On pourrait croire qu’elles ne revêtent pas beaucoup d’importance, mais elles exigent le même soin que les étapes précédentes, car elles peuvent avoir un effet déterminant non seulement sur la conception, mais aussi sur la planification et le budget du projet.
1.8.1.1. Transport
Le transport s’effectue généralement par route. Les règles de circulation variant d’un pays à l’autre, elles peuvent avoir une incidence sur les dimensions indiquées ci-dessous.
Les éléments ne mesurant pas plus de 9-10 m de long peuvent être transportés par des camions ordinaires. Les éléments qui mesurent plus de 12 m de long doivent être transportés sur des semi-remorques dotées d’un plateau télescopique. Ce système permet de transporter des éléments mesurant jusqu’à 30-35 m de long. Dans le cas de poutres longues en petite quantité, ce type de transport revient cher ; il est donc préférable de les diviser en sections plus courtes transportables par un camion normal.
Les véhicules longs nécessitent une autorisation spéciale des autorités. Les éléments ne dépassant pas 25-30 m de long ne posent généralement pas problème. La longueur maximale admise sans autorisation spéciale varie selon les pays, mais elle est généralement de 25 m environ. En principe, un transport spécial est nécessaire lorsque l’élément fait plus de 2,5 m de large ou 4,5 m de haut, ce qui est souvent le cas des portiques ou des arcs. Le transport ferroviaire ou maritime est également possible, mais impose d’autres limites. Les problèmes de transport peuvent généralement être palliés en divisant la structure en plusieurs sections adaptées au transport, qui sont ensuite assemblées sur le lieu de construction.
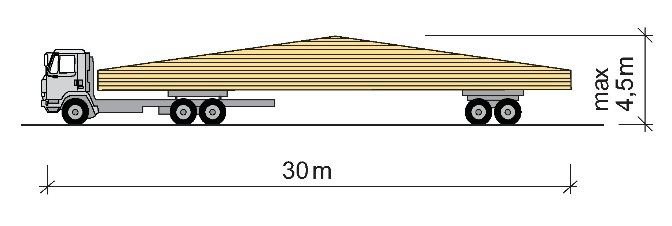
Figure 1.20 : La longueur et la hauteur maximales autorisées pour les véhicules ne disposant pas d’une autorisation spéciale varient selon les pays.
1.8.1.2. Montage
Le montage des structures en bois lamellé-collé nécessite presque toujours l’utilisation d’un appareil de levage (en principe une grue mobile).
La meilleure solution consiste à hisser l’élément lamellé-collé directement du camion à sa place dans le bâtiment. Ceci est néanmoins rarement possible et en règle générale, un certain temps de stockage sur le lieu de construction est nécessaire. Les instructions indiquées précédemment doivent, dans ce cas, être suivies.
Au moment de la livraison, il convient de vérifier si le nombre d’éléments lamellés collés et d’organes d’assemblage est conforme à la commande.
Il est important de planifier le montage avant de décharger les éléments lamellés collés pour éviter de perdre du temps en rechargement. Le marquage clair et systématique de chaque élément lamellé-collé et des organes d’assemblage est également important pour accomplir le montage avec efficacité.
Tant que le système de stabilisation du bâtiment n’est pas achevé, des mesures temporaires doivent être prises pour que la structure résiste au vent et aux autres charges pendant toute la durée de la construction. Des câbles d’acier tendus à l’aide de tendeurs à lanterne constituent le meilleur moyen de fixer les portiques et les arcs. Les câbles sont également utilisés pour positionner correctement la structure avant la mise en place de la charpente de comble ou de tout dispositif similaire.
Les emballages en plastique des poutres doivent être ouverts par le dessous pour empêcher l’humidité de pénétrer. L’emballage peut aussi être complètement retiré, mais les éléments visibles risquent alors d’être salis lors du montage. Les charpentes de comble qui consistent en des tôles ondulées posées directement sur les poutres sont particulièrement vulnérables, car l’eau qui s’écoule par les joints des tôles peut décolorer les côtés des poutres avant que l’isolation et le carton-feutre bitumé soient mis en place.
Les portiques et les arcs à trois rotules sont composés de deux parties qui sont raccordées aux fondations en béton ou aux poteaux et sont reliées l’une à l’autre à l’aide d’éléments de fixation en acier fixés au faîtage. L’utilisation d’une grue mobile et d’une tour d’assemblage amovible sous le faîtage permet d’assembler facilement et dans de bonnes conditions de sécurité les structures de grande taille. Lors du montage, chaque moitié de portique ou d’arc est hissée et mise en place à l’aide d’une grue mobile. Le pied ou le point le plus bas est fixé à un élément de fixation ou à la tête d’un poteau et l’extrémité supérieure est placée sur la tour, où elle est reliée à l’autre moitié, préalablement hissée et mise en place de la même façon. Dès que le contreventement est en place, la tour d’assemblage est déplacée vers l’unité suivante et le processus est répété.
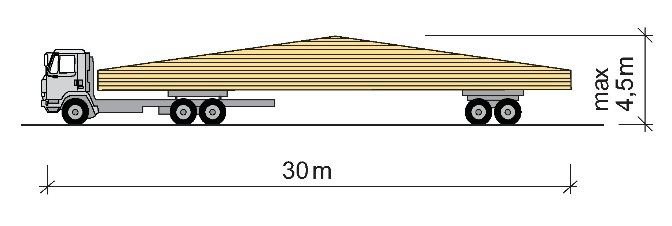
Figure 1.20 : La longueur et la hauteur maximales autorisées pour les véhicules ne disposant pas d’une autorisation spéciale varient selon les pays.
1.8.2. Commande et livraison
1.8.2.1. Spécifications
Les éléments suivants doivent être indiqués sur les plans et dans les spécifications :
› Code d’identification (par exemple B1, P3, etc.)
› Type d’élément (par rapport au plan par exemple)
› Dimension nominale (largeur x hauteur au niveau de l’appui gauche/hauteur maximale/hauteur au niveau de l’appui droit x longueur en mm) Pour les poutres et poteaux à hauteur constante, seule une hauteur doit être indiquée. Pour les éléments spéciaux (poutre à double décroissance asymétrique, par exemple), les dimensions doivent figurer sur un plan.
› Classe de résistance
› Type d’adhésif (I ou II conformément à la norme EN 14080)
› Finition de surface (indiquer au besoin les côtés laissés visibles)
› Traitement de surface (le cas échéant)
› Contre-flèche (le cas échéant)
› Essences de bois (autres que l’épicéa ; pin traité sous pression par exemple)
› Déviations autorisées.
Exemple de spécifications : 4 poutres à double décroissance 165 x 680/1370/680 x 22000 mm, GL24h/type I, surfaces proprement rabotées – Contre-flèche : 120 mm.
Au moment d’établir un devis ou de passer une commande, il convient également d’indiquer les éléments suivants :
› Nombre d’unités identiques (à noter qu’un portique à trois rotules ou un arc à trois rotules se compose de deux éléments)
› Référence éventuelle à un plan montrant les trous, les entailles, etc.
› Exigences particulières concernant l’emballage (emballage individuel, protection des bords, etc.)
› Calendrier de livraison › Détails relatifs au déchargement (grue ou appareil de chargement)
› Nom et adresse correspondant au projet
1.8.2.2. Cotation
Une cotation claire et précise facilite la fabrication et réduit le risque d’erreurs.
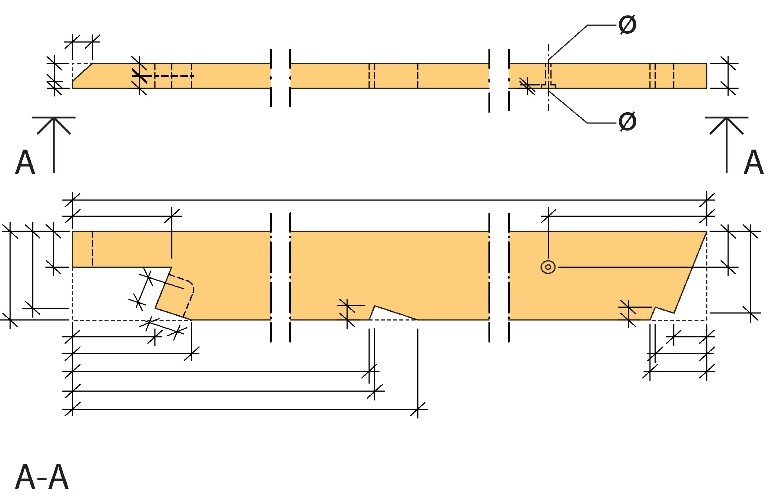
Figure 1.21 : Exemple de cotation.